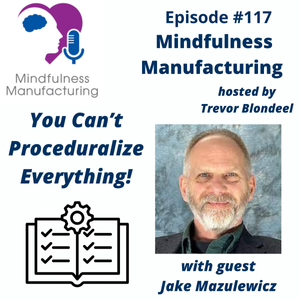
117 You Can’t Proceduralize Everything! With Jake Mazulewicz
05/15/24 • 30 min
When a mistake occurs on the plant floor, your mind might jump to one question: who caused this issue, and should I write them up for their mistake? But there’s a more productive approach you could be taking—and in this episode of Mindfulness Manufacturing, guest Dr. Jake Mazulewicz breaks it all down!
With a background as a firefighter, EMT, and military paratrooper, Jake knows the challenges of high-hazard industries, and works with organizations to reduce errors and create safer, more reliable workplace environments. In this episode, Jake shares why you can’t procedularize everything, including the way you handle errors and accidents, and offers great insights and stories about how to use connection and curiosity to improve safety, address errors, and strengthen your organization.
3:35 – Procedures and policies are the work that is imagined, and on the floor is how the work actually gets done
4:19 – The work as-done is almost always radically different than the work as-imagined
5:20 – Even when you have standards and people show up wanting to do a good job, you can still see issues that need to be addressed
6:44 – There will always be areas that absolutely need to have procedures in place
8:02 – There are also adaptive jobs, which leans less into procedures and more intro troubleshooting and tacit human knowledge
10:56 - In an ideal environment, both mechanistic and adaptive models are used and respected and needed
12:11 – There are four levels, ranging from strict procedurals to looser guidelines that show what to do, but not how to do it
15:36 – Tacit knowledge gets shared through conversations
16:22 – A way to share important information is to have frontline experts record videos sharing their insights to problems, especially those that are not covered in procedures
19:44 – Through conversation and connection, more knowledge is shared
21:58 – Debriefing also plays a central role
23:45 – If you have strong discipline, you’ll find more freedom
25:31 – In most situations, errors are signals, not defects
27:07 – When an error occurs, be curious and find the deeper cause of the problem
Connect with Jake Mazulewicz
Find him on Linkedin
Visit his website
When a mistake occurs on the plant floor, your mind might jump to one question: who caused this issue, and should I write them up for their mistake? But there’s a more productive approach you could be taking—and in this episode of Mindfulness Manufacturing, guest Dr. Jake Mazulewicz breaks it all down!
With a background as a firefighter, EMT, and military paratrooper, Jake knows the challenges of high-hazard industries, and works with organizations to reduce errors and create safer, more reliable workplace environments. In this episode, Jake shares why you can’t procedularize everything, including the way you handle errors and accidents, and offers great insights and stories about how to use connection and curiosity to improve safety, address errors, and strengthen your organization.
3:35 – Procedures and policies are the work that is imagined, and on the floor is how the work actually gets done
4:19 – The work as-done is almost always radically different than the work as-imagined
5:20 – Even when you have standards and people show up wanting to do a good job, you can still see issues that need to be addressed
6:44 – There will always be areas that absolutely need to have procedures in place
8:02 – There are also adaptive jobs, which leans less into procedures and more intro troubleshooting and tacit human knowledge
10:56 - In an ideal environment, both mechanistic and adaptive models are used and respected and needed
12:11 – There are four levels, ranging from strict procedurals to looser guidelines that show what to do, but not how to do it
15:36 – Tacit knowledge gets shared through conversations
16:22 – A way to share important information is to have frontline experts record videos sharing their insights to problems, especially those that are not covered in procedures
19:44 – Through conversation and connection, more knowledge is shared
21:58 – Debriefing also plays a central role
23:45 – If you have strong discipline, you’ll find more freedom
25:31 – In most situations, errors are signals, not defects
27:07 – When an error occurs, be curious and find the deeper cause of the problem
Connect with Jake Mazulewicz
Find him on Linkedin
Visit his website
Previous Episode
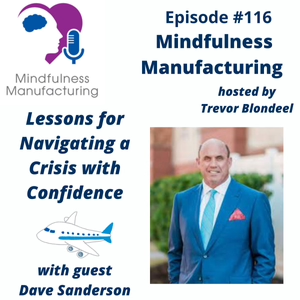
116 Lessons for Navigating a Crisis with Confidence with Dave Sanderson
In 2009, total engine loss forced US Airways Flight 1549 to make an emergency crash landing in New York City’s Hudson River—and thanks to the quick actions of the pilot, flight crew, and passengers, all 155 people on board made it safely off the plane. Now known as “the miracle on the Hudson,” this harrowing incident offers up important lessons on staying calm under pressure, coping with traumatic challenges, and making every moment count.
To learn more, let’s hear from a Flight 1549 survivor! Dave Sanderson is a nationally recognized leadership speaker and bestselling author, who draws from his inspirational story of survival to encourage others to do the right thing and find healthy ways to cope with their own struggles and adversity. In this episode of Mindfulness Manufacturing, Dave shares his own Miracle on the Hudson story, and offers powerful insights he learned from being the last passenger off Flight 1549!
2:18 – Dave shares his Flight 1549 story
8:11 – In times of conflict, whether it’s a plane crash or issue on the manufacturing floor, calmness and confidence play key roles
9:05 – To get through challenging situations, you need to manage your own mindset
10:05 – You don’t need to know everything to handle a crisis, but you have to be able to lead yourself first
11:09 – Every moment in your life happens for a reason
13:38 – How to react to and cope with a challenging situation depends on the meaning you attach to it
14:22 – By reframing the meaning you attach to a situation, you can find healthy and productive ways to react and grow
15:33 – Everyone assigns different meanings to different challenges, so it’s important to approach others with curiosity instead of judgement
17:56 – To truly understand others, you need be curious and have authentic interactions
21:52 – To feel included in an organization’s mission, people need and want certainty, variety, connection, significance, growth, and the ability to contribute
24:48 – As a leader, it’s up to you to find creative solutions and create opportunity from challenges
28:57 – If you get casual, it can lead to safety issues, accidents, and other serious problems for your organization
Connect with Dave Sanderson
Check out his website and download a free copy of his Moments Matter Magazine
Connect on LinkedIn to see new blog content
Next Episode
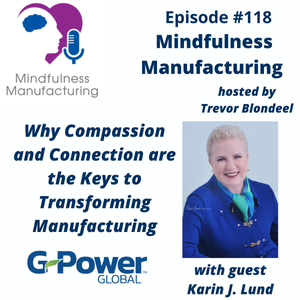
118 Why Compassion and Connection are the Keys to Transforming Manufacturing with Karin J. Lund
The manufacturing industry just keeps getting greater—and it’s all thanks to passionate, mindful leaders who show up every day ready to engage their teams, improve their mindset, and create an environment where people love to work. One of these leaders is Karen J. Lund, a bestselling author and keynote speaker with a long career in the steel industry. Drawing on her experience in the steel industry, Karin now leads the team at G-Power Global, an organization she founded to inspires corporate and organizational entities to lead with compassion while continuing to focus on productivity, service, and profits.
In this episode, Karin talks more about transformations facing the steel industry and manufacturing as a whole, and shares why compassion, connection, and conversations are the key to unlocking creative solutions, overcoming challenges, and bringing new energy to the manufacturing floor.
3:03 – In manufacturing, you can’t do everything by yourself, which makes it very important to seek out and build strong connections
5:33 – It can be a challenge to form relationship on the floor, especially for younger professionals
6:48 – When people have connections on the floor, it makes it easier to voice feedback and navigate challenges
9:01 – By creating a culture that fosters connections and conversation, you’ll find more productivity and more creative solutions
11:37 – Compassion is the competitive edge
15:55 – There is a difference between training and learning
16:39 – Employee resource groups are a strong tool for building connections and community in the workplace
19:20 – If you want to redefine your industry and image, start by having conversations about your values and how you present to the media and others
22:25 – In manufacturing, it’s important to have conversations about how your role impacts the work of others, and vice versa
23:29 – Everyone learns in different ways and some people may need different accommodations
25:02 – When someone makes a commitment to their industry, it can have a positive impact for entire teams and organizations
Connect with Karin J. Lund
Thanks for Listening!
Thanks for tuning it to another episode of Mindfulness Manufacturing! To learn more about Trevor Blondeel and Manufacturing Greatness, please visit our website or contact Trevor here.
If you like this episode you’ll love
Episode Comments
Generate a badge
Get a badge for your website that links back to this episode
<a href="https://goodpods.com/podcasts/mindfulness-manufacturing-512498/117-you-cant-proceduralize-everything-with-jake-mazulewicz-67065863"> <img src="https://storage.googleapis.com/goodpods-images-bucket/badges/generic-badge-1.svg" alt="listen to 117 you can’t proceduralize everything! with jake mazulewicz on goodpods" style="width: 225px" /> </a>
Copy