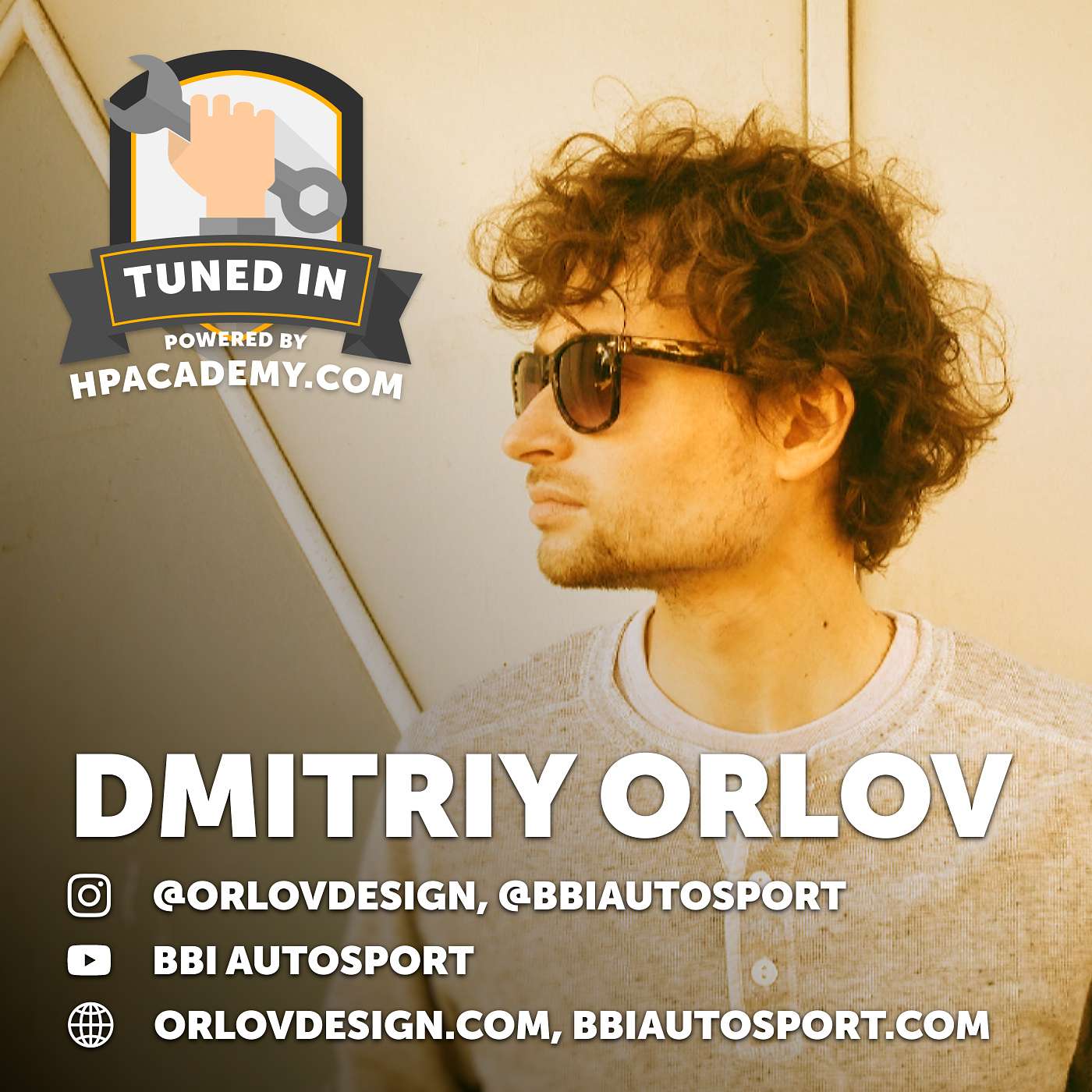
118: Spend Less Time & Money On Your Build.
07/04/24 • 129 min
If you’re planning a big race or street car build, it’s worth thinking about how you can harness the power of 3D scanning, CAD, and additive manufacturing on the big jobs.
In this episode, BBi Autosport’s Dmitriy Orlov explains how you can incorporate these tools into your build process, how he utilised them when building the infamous “Hoonipigasus” Porsche 911, and a whole lot more.
Use “ORLOV50” to get $50 OFF your 3D Modelling & CAD for Motorsport course: https://hpcdmy.co/CADb
BBi Autosport is one of the best known aftermarket Porsche specialists out there, pumping out a range of high-quality parts and builds over the last decade. Based at the company’s California facility, Dmitriy is the product development engineer behind it all, despite not having the educational background in mechanical engineering that you might expect of someone in his line of work.
Dmitriy is self taught, and that gives him a unique perspective on design and manufacturing. He talks us through his design process, and discusses how far technology has come in the last few years — both in terms of what it can achieve and how accessible it’s become to the home enthusiast. Dmitriy explains how the average person can harness all this tech to drastically trim down the amount of time and money being spent on a serious race or street car build.
This then gets us on to the topic of 3D printing final parts in metal, and Dimitri dives into just how useful this technology has become. As he points out — sure, you might not have the capability to print metal at home, but it’s now becoming viable to send your design to a third party which can then create the part using its own multi-million dollar printers.
The conversation then moves on to Dmitriy's most well-known project, the “Hoonipigasus” Porsche 911 hillclimb monster. This is a car that most people will be aware of and think they know a lot about, however Dmitriy is able to give us some really interesting insights into the build, its immense challenges, and how he and his team overcame those challenges.
Follow Dmitriy and BBi Autosport here:
IG: @orlovdesign, @bbiautosport
YT: BBi Autosport
WWW: orlovdesign.com, bbiautosport.com
Don’t forget, you can use “ORLOV50” to get $50 OFF your 3D Modelling & CAD for Motorsport course: https://hpcdmy.co/CADb
Timestamps:
4:06 How did you become passionate about the automotive industry?
8:15 How did you learn your skillset?
9:57 Does having shop floor experience make you a better designer?
11:42 Are there any drawbacks to not having an engineering degree?
15:51 When did you start diving into 3D modelling and CAD?
20:32 What are the steps from CAD model to actually machining a physical part
23:10 What did you do before working for BBI and what is BBI?
32:28 Design process.
43:06 Choosing the right manufacturing process for the part.
51:07 Designing a manifold not just for 1000hp, but to fit and work on a factory vehicle.
58:05 How has 3D scanning changed things for BBI?
1:06:40 Are there affordable scanners that are worth buying?
1:12:10 What CAD software do you use and why?
1:20:46 Do you use FEA?
1:27:18 What is the Hoonipigisus?
1:31:15 Engine and gearbox configuration.
1:34:28 Biggest challenge?
1:38:49 Challenge of running a drive shaft from a rear trans to front differential?1:41:30 How much of a disadvantage would it have been rear wheel drive?
1:48:50 Are there any key aspects you’d do differently?
If you’re planning a big race or street car build, it’s worth thinking about how you can harness the power of 3D scanning, CAD, and additive manufacturing on the big jobs.
In this episode, BBi Autosport’s Dmitriy Orlov explains how you can incorporate these tools into your build process, how he utilised them when building the infamous “Hoonipigasus” Porsche 911, and a whole lot more.
Use “ORLOV50” to get $50 OFF your 3D Modelling & CAD for Motorsport course: https://hpcdmy.co/CADb
BBi Autosport is one of the best known aftermarket Porsche specialists out there, pumping out a range of high-quality parts and builds over the last decade. Based at the company’s California facility, Dmitriy is the product development engineer behind it all, despite not having the educational background in mechanical engineering that you might expect of someone in his line of work.
Dmitriy is self taught, and that gives him a unique perspective on design and manufacturing. He talks us through his design process, and discusses how far technology has come in the last few years — both in terms of what it can achieve and how accessible it’s become to the home enthusiast. Dmitriy explains how the average person can harness all this tech to drastically trim down the amount of time and money being spent on a serious race or street car build.
This then gets us on to the topic of 3D printing final parts in metal, and Dimitri dives into just how useful this technology has become. As he points out — sure, you might not have the capability to print metal at home, but it’s now becoming viable to send your design to a third party which can then create the part using its own multi-million dollar printers.
The conversation then moves on to Dmitriy's most well-known project, the “Hoonipigasus” Porsche 911 hillclimb monster. This is a car that most people will be aware of and think they know a lot about, however Dmitriy is able to give us some really interesting insights into the build, its immense challenges, and how he and his team overcame those challenges.
Follow Dmitriy and BBi Autosport here:
IG: @orlovdesign, @bbiautosport
YT: BBi Autosport
WWW: orlovdesign.com, bbiautosport.com
Don’t forget, you can use “ORLOV50” to get $50 OFF your 3D Modelling & CAD for Motorsport course: https://hpcdmy.co/CADb
Timestamps:
4:06 How did you become passionate about the automotive industry?
8:15 How did you learn your skillset?
9:57 Does having shop floor experience make you a better designer?
11:42 Are there any drawbacks to not having an engineering degree?
15:51 When did you start diving into 3D modelling and CAD?
20:32 What are the steps from CAD model to actually machining a physical part
23:10 What did you do before working for BBI and what is BBI?
32:28 Design process.
43:06 Choosing the right manufacturing process for the part.
51:07 Designing a manifold not just for 1000hp, but to fit and work on a factory vehicle.
58:05 How has 3D scanning changed things for BBI?
1:06:40 Are there affordable scanners that are worth buying?
1:12:10 What CAD software do you use and why?
1:20:46 Do you use FEA?
1:27:18 What is the Hoonipigisus?
1:31:15 Engine and gearbox configuration.
1:34:28 Biggest challenge?
1:38:49 Challenge of running a drive shaft from a rear trans to front differential?1:41:30 How much of a disadvantage would it have been rear wheel drive?
1:48:50 Are there any key aspects you’d do differently?
Previous Episode
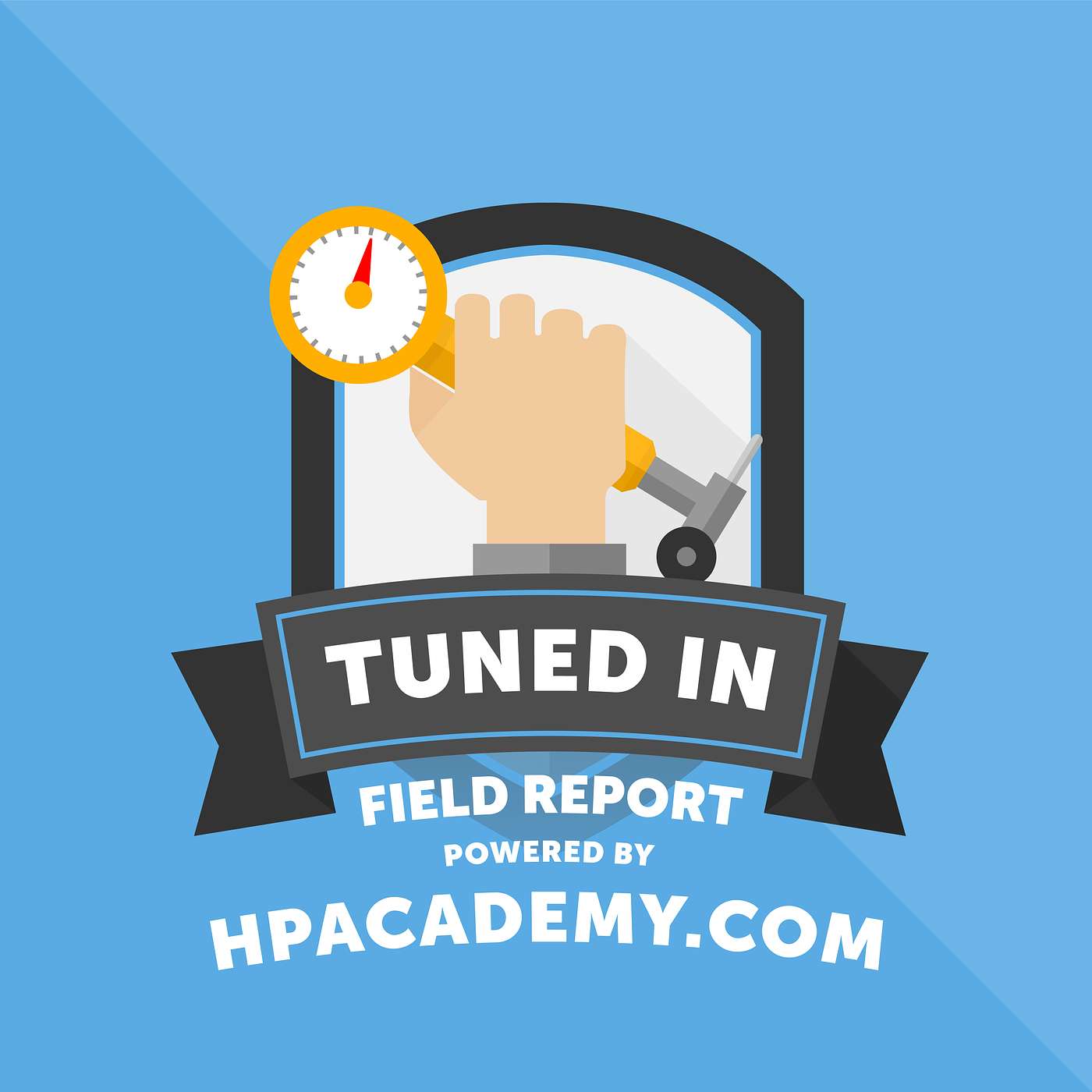
Field Report: What IS this thing!?!
Why does this 800hp car look like it belongs to racing classic DTM cars, and what's up with the 6 cylinders?
Aleck Kazakovski of GotItRex explains some of the tech talk story of how this GC8/Type R STi has grown into the monster it is today, with multiple time attack wins in Australia and a unique but well-proven setup.
The turbocharged EG33 is capable of 9,500rpm and 750kw (1000hp) at 40 PSI, but the team dials things back in the interests of reliability and wallet health to a 'modest' 600kw (800hp) at 25 PSI and a 9,000rpm limit. Madness!
There isn't much that hasn't been touched on the EG33 to make this happen, including being bored and stroked with extensive headwork to give a very usable powerband with full boost from 4,500 rpm. Lubrication is handled by a custom GIR dry sump setup using existing off-the-shelf components. Clever!
An EMtron electronics package helps keep it all working as intended, and a Modena sequential transmission package puts the power to the ground without turning into Swiss cheese as you would expect the OEM Subaru parts to; however, OEM housings and much of the physical placements are retained or at least are very close to where they were which keeps some of the heritage rather than being a complete Frankensteins monster. No doubt, this also enables an easy time with spares and repairs.
A PE Racing pedal box and AP Racing calipers and rotors help haul the car up for the corners, with Aleck and the team opting to avoid some of the oversized rear brake issues many Subaru owners fall into the trap of, and ABS is on the cards for the future to help leverage the system further.
Next Episode
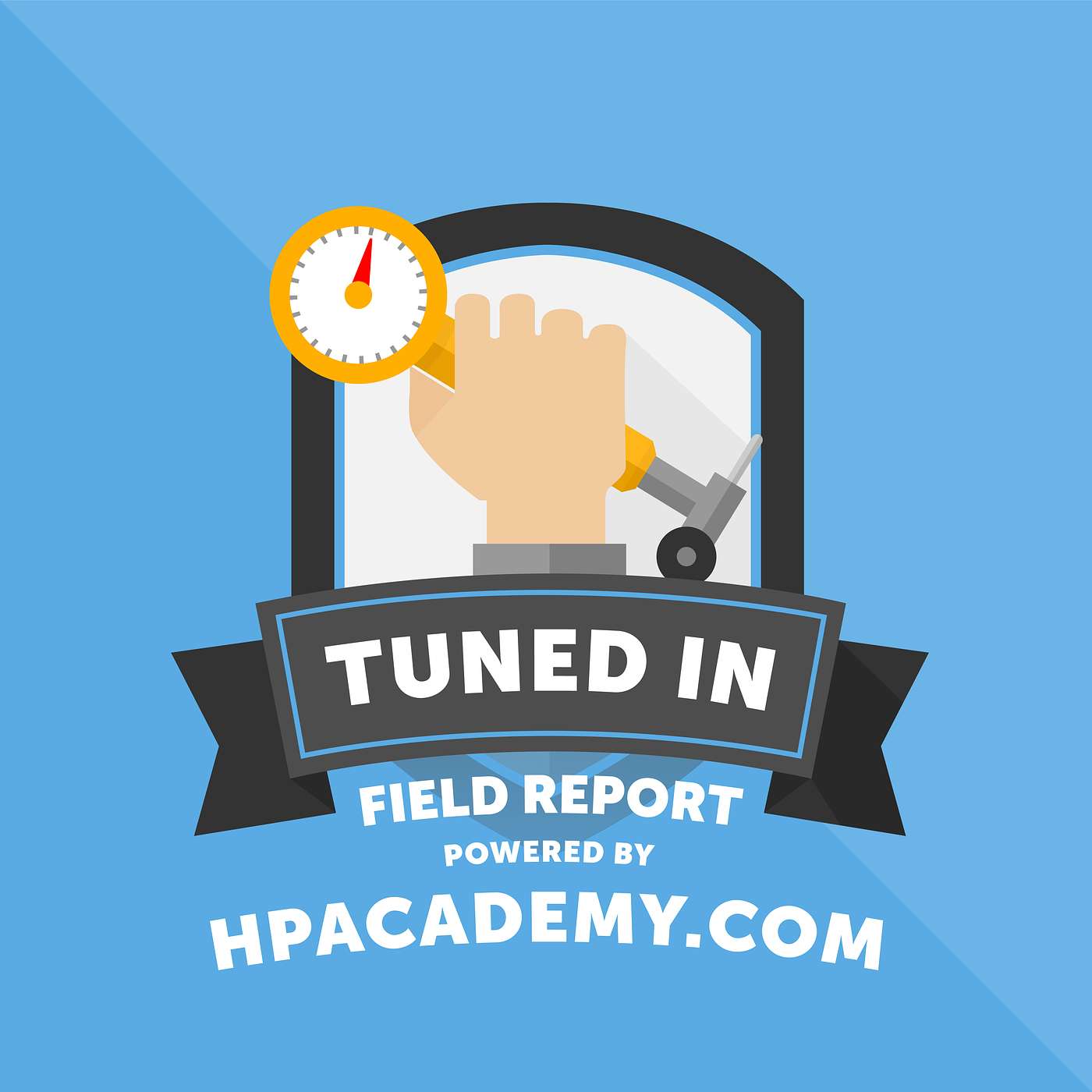
Field Report: 4 Rotor Build Out, 7.4L N/A V8 In.
Quad Rotor vs V8, Procharger vs Natural Aspiration and more.
Use ‘PODCAST75’ for $75 off your first HPA course here: https://hpcdmy.co/hpa-tuned-in
It's hard to nail form and function, but Carl Thompson has it down to a fine art when it comes to drift builds between his old 1300HP 26B 4-rotor Aristo/GS300 build and this high compression 'small block' @Mast Motorsports 454ci (7.4L) LSX based V8 Nissan S15 Silva one that is another work of art. Even if you are a solid rotary fan it's hard not to appreciate the same level of detail and perfection that has gone into this LS-based S15 build.
We'll discuss why Carl moved away from his 4 rotors (one of which now powers Rob Dahms AWD RX7 build) and towards the MoTeC M130-controlled LS V8 platform as he has gotten more serious about competing and doing full-season campaigns along with why he chose a naturally aspirated setup despite having a procharger bolted on at some point in time.
The difference in power levels required for D1NZ and US series also pops up as well as the performance increases gained from his Dailey Engineering dry sump system and what the main driver displays and warnings he pays attention to during a competition run and interestingly why he went with a cast-iron LSX based block over the aluminium LS(x) blocks that are also able to handle sizeable power figures.
00:00 Intro
00:25 Rotary Vs LSX
01:31 Engine Specs
02:10 Iron Vs Alloy Decision
03:35 Procharger Vs N/A
05:06 Procharger Powerband
06:08 Dry Sump Setup
07:02 30HP+ From Good Vacuum
08:49 @MoTeCAustralia ECU, Indiindividual cylinder fuel delivery
10:55 Dash Display Settings
12:21 Drivetrain
14:00 Diff, Suspension
To get power to the ground the car runs a Holinger Engineering RD6 sequential, Tilton bell housing, flywheel and triple-plate carbon clutch leading to the Winters 25cm IRS quick-change and 35-spline stub axles.
A MoTeC M130, PDM30 and C125 logger/dash display and EMtron ETC4’s (for individual cylinder monitoring) round up the electronics side of things and giving Carl the ability to clutchless shift off the line.
If you like this episode you’ll love
Episode Comments
Generate a badge
Get a badge for your website that links back to this episode
<a href="https://goodpods.com/podcasts/tuned-in-197122/118-spend-less-time-and-money-on-your-build-59563777"> <img src="https://storage.googleapis.com/goodpods-images-bucket/badges/generic-badge-1.svg" alt="listen to 118: spend less time & money on your build. on goodpods" style="width: 225px" /> </a>
Copy