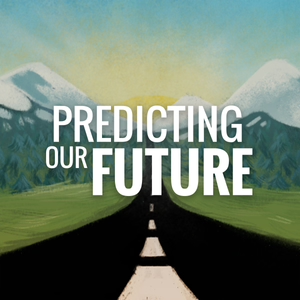
Episode 4: NYC Goes Modular
03/29/17 • 30 min
In the summer of 2016, the world’s tallest modular building at 32 stories high was completed at 461 Dean Street in Brooklyn, NY. Once the building’s apartment modules were completed at a factory located in the Brooklyn Navy Yard, they were transported to the development site and essentially stacked one on top of another into a high-rise building. To the dismay of its original backers, the building was delivered years late, riddled with construction problems, and the subject of a costly litigation. Still, excitement about modular construction in New York abounds with new projects under development.
Sponsored by:
If you’re a startup, apply for DigitalOcean’s Hatch program, where if selected, you’ll have access to their cloud for 12 months, in addition to technical training and mentorship. You can also go to do.co/predictingourfuture and ask the sales team for a free trial.
Interviewees
Episode Excerpt
U.S. Multi-Family Building
If you were paying any attention to the 2016 U.S. presidential election, you would think that just about every factory in the United States has either left for China or is about to leave. But when it comes to factories that are currently building apartments, or will soon be building apartments, we’re probably just getting started with constructing these factories in the United States.S hipping costs make transporting building modules from overseas to the United States expensive. And while one Polish company has managed to successfully transport modules here, the transportation expense is likely to make this a predominantly local industry. That, along with undeniable demographic shifts afoot in the United States that will be pushing the demand much higher for multi-family buildings in urban areas, suggest that we may very well witness the transformation of American factory-built construction into a multi-billion dollar industry.
Based on what world populations and growth rates suggest, you might think that the urgent need for urban housing over the next 30 years will largely be an African and Asian phenomenon. But the truth is that the migration to cities is also expected to happen right here at home. The United States Census Bureau provides statistics on the number of permits issued for new construction starts each year throughout the entire country. In 2015, 41% of permits were issued for structures that consisted of two or more units (referred to as a “multi-family residence”). Not exactly a screaming validation of my argument that you should be building modular multi-family buildings in cities when 59% of permits were for single-family residences.
But let’s look at the trend line towards multi-family construction over the past 25 years. Again, from the United States Census Bureau’s website:
- In 1991, 21% of permits were for multi-family residences;
- In 2000, 25% of permits were for multi-family residences;
- In 2007, 30% of permits were for multi-family residences;
- And again, in 2015, 41% of permits were for multi-family residences.
The rising trend of multi-family starts, as a percentage of total building starts, is unmistakeable. Here’s another interesting set of facts. The U.S. Census Bureau breaks down the multi-family residence into three categories: two units; three and four units; and five units and up:
In 1991, 79% of the multi-family category permits were for buildings with five plus units;
By 2015, 93% of permits in the multi-family category were for buildings with five plus units.
As it turns out, if you’re an entrepreneur and thinking about factory-built housing in the United States, the biggest market to go after today is single-family homes. But if the trend towards urban development continues, the biggest market to attack will soon be for multi-family homes. In New York City, two companies began with a modular approach, meaning they were building boxes inside of factories that would be stacked one on top of another once they arrived on the jobsite.
Brooklyn
New York City’s population is growing. In 2014, the city was home to just under 8.5 million people. By 2030, we’re expected to surpass 9 million people. In 2016 alone, New York City will add a total of 24,575 new apartments. My home in Brooklyn will lead all the other boroughs with over 6,000 new units.
At the end of this podcast series on factory-built housing, I’ll make some predictions about what the future will look like and who will be the winners in this space. Without giving it all away, I can tell you who I don’t expect to be the agents of massive change: billionaire New York real estate developers. And tha...
In the summer of 2016, the world’s tallest modular building at 32 stories high was completed at 461 Dean Street in Brooklyn, NY. Once the building’s apartment modules were completed at a factory located in the Brooklyn Navy Yard, they were transported to the development site and essentially stacked one on top of another into a high-rise building. To the dismay of its original backers, the building was delivered years late, riddled with construction problems, and the subject of a costly litigation. Still, excitement about modular construction in New York abounds with new projects under development.
Sponsored by:
If you’re a startup, apply for DigitalOcean’s Hatch program, where if selected, you’ll have access to their cloud for 12 months, in addition to technical training and mentorship. You can also go to do.co/predictingourfuture and ask the sales team for a free trial.
Interviewees
Episode Excerpt
U.S. Multi-Family Building
If you were paying any attention to the 2016 U.S. presidential election, you would think that just about every factory in the United States has either left for China or is about to leave. But when it comes to factories that are currently building apartments, or will soon be building apartments, we’re probably just getting started with constructing these factories in the United States.S hipping costs make transporting building modules from overseas to the United States expensive. And while one Polish company has managed to successfully transport modules here, the transportation expense is likely to make this a predominantly local industry. That, along with undeniable demographic shifts afoot in the United States that will be pushing the demand much higher for multi-family buildings in urban areas, suggest that we may very well witness the transformation of American factory-built construction into a multi-billion dollar industry.
Based on what world populations and growth rates suggest, you might think that the urgent need for urban housing over the next 30 years will largely be an African and Asian phenomenon. But the truth is that the migration to cities is also expected to happen right here at home. The United States Census Bureau provides statistics on the number of permits issued for new construction starts each year throughout the entire country. In 2015, 41% of permits were issued for structures that consisted of two or more units (referred to as a “multi-family residence”). Not exactly a screaming validation of my argument that you should be building modular multi-family buildings in cities when 59% of permits were for single-family residences.
But let’s look at the trend line towards multi-family construction over the past 25 years. Again, from the United States Census Bureau’s website:
- In 1991, 21% of permits were for multi-family residences;
- In 2000, 25% of permits were for multi-family residences;
- In 2007, 30% of permits were for multi-family residences;
- And again, in 2015, 41% of permits were for multi-family residences.
The rising trend of multi-family starts, as a percentage of total building starts, is unmistakeable. Here’s another interesting set of facts. The U.S. Census Bureau breaks down the multi-family residence into three categories: two units; three and four units; and five units and up:
In 1991, 79% of the multi-family category permits were for buildings with five plus units;
By 2015, 93% of permits in the multi-family category were for buildings with five plus units.
As it turns out, if you’re an entrepreneur and thinking about factory-built housing in the United States, the biggest market to go after today is single-family homes. But if the trend towards urban development continues, the biggest market to attack will soon be for multi-family homes. In New York City, two companies began with a modular approach, meaning they were building boxes inside of factories that would be stacked one on top of another once they arrived on the jobsite.
Brooklyn
New York City’s population is growing. In 2014, the city was home to just under 8.5 million people. By 2030, we’re expected to surpass 9 million people. In 2016 alone, New York City will add a total of 24,575 new apartments. My home in Brooklyn will lead all the other boroughs with over 6,000 new units.
At the end of this podcast series on factory-built housing, I’ll make some predictions about what the future will look like and who will be the winners in this space. Without giving it all away, I can tell you who I don’t expect to be the agents of massive change: billionaire New York real estate developers. And tha...
Previous Episode
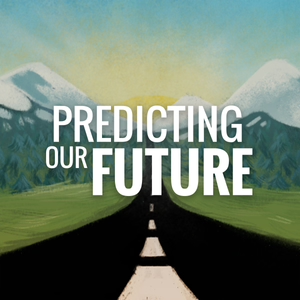
Episode 3: Google, China, & Overnight Cities
If a trillion dollar market opportunity exists, you can bet the people at Google are thinking about it. Within X, Google’s most secretive lab, they’ve been working on solving the problem of how to make building construction more efficient in order to deal with the world’s severe and worsening urban housing shortage. By the year 2050, the global population is expected to grow by 2.2 billion people, and 90% of that growth is expected to take place in cities that are in dire need of new housing. In China, one company has figured out how to deal with this challenge by prefabricating components for skyscrapers inside of a factory.
Sponsored by:
If you’re a startup, apply for DigitalOcean’s Hatch program, where if selected, you’ll have access to their cloud for 12 months, in addition to technical training and mentorship. You can also go to do.co/predictingourfuture and ask the sales team for a free trial.
Interviewees
Episode Excerpt
Google & Flux
When you hear the word Google, you first and foremost associate it with search. You have a disagreement with someone: let’s Google it. You want to know where to vacation: Google it. You want to know what a company does: Google it.
But if you’ve been watching Google over the years, you know that Google does much more, than well, Google. There’s Gmail and Google Hangouts and Google Apps and Google Drive. The relationship between these offshoots became so obvious that Google just decided to brand them collectively as the “G Suite.” Somewhere along Google’s path of phenomenal success, the company decided to start working on some super interesting and hard problems that are really unrelated to the company’s initial mission of organizing the world’s information. The founders of Google have become so invested in developing other businesses that the company is no longer called Google. In January of 2016, the company was renamed Alphabet, with Google becoming just one of their subsidiaries.
Calico is Alphabet’s biotech subsidiary that is focused on extending human life. Verily is Alphabet’s life sciences subsidiary. One of their projects is to develop contact lenses for diabetics that are able to determine when a person’s glucose levels are running high. And then there is Google X, now referred to simply as “X,” the secretive think tank within Alphabet pioneering projects like the driverless car that will one day make the act of driving obsolete.
On the website for X, the mission statement reads: “We’re a moonshot factory. Our mission is to invent and launch ‘moonshot’ technologies that we hope could someday make the world a radically better place.” Google can be very secretive about their work, and this is ground zero for where their secret projects are born. X’s stealth projects have one of three outcomes: they are elevated to a division within Google and made public, they are spun out to become a separate stand-alone company, or they are killed.
To date, the only company to ever come out of X and be spun out into a separate entity is Flux. I spoke with Jen Carlile, a Co-founder of Flux, who initially joined Google as a software engineer in 2010.
Jen Carlile: “The way that Google X works is they identify what they call ‘world scale problems’ and then put a group of smart people together and say, ‘try to come up with a solution for this that can be tackled within a 10 year time horizon.’ So our big hairy problem was urban population growth. And the Google X leadership recognized that the pace at which we’re building buildings and with the way that we do it now, we’re simply not going to be able to keep up with urban population growth.”
In 1803, just 3% of the world’s population resided in urban areas. I have this romantic image of living in the 18th century in a glamorous European city. But as it turns out, if you lived in a city in the early 1800’s, you were part of a minority. This was before the Industrial Revolution had caused massive migrations from the country to cities where factories were located. The result of these massive migrations? By 1900, 14% of the world’s population was living in cities. In 1950, the percentage of the world’s population that lived in cities was 30%. And then in 2008, for the first time in the history of the world, the percentage of people living in cities equaled the percentage of people who lived outside of cities.
Here’s where it gets interesting. As of 2016, there are 7.4 billion people on the planet. 2.2 billion people are expected to join us by the year 2050, and 90% of this growth is expected to take place in cities.
It’s really hard to make sense of what the...
Next Episode
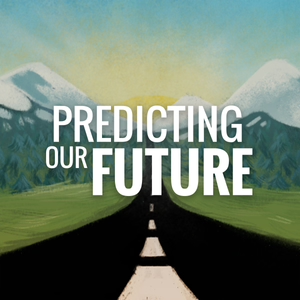
Episode 5: Cars, Mars, & 3D Printing
In 2012, six single-family homes were made by a 3D printer in China. The inventor of that technology is now working on a 3D printer designed to construct buildings on Mars. Does this technology have a future on Earth? Or does the future of homebuilding involve modern factories that leverage robots to build wood or steel framing similar to the types of machines you might find in modern automotive plants?
Sponsored by:
If you’re a startup, apply for DigitalOcean’s Hatch program, where if selected, you’ll have access to their cloud for 12 months, in addition to technical training and mentorship. You can also go to do.co/predictingourfuture and ask the sales team for a free trial.
Interviewees
Episode Excerpt
3D-Printed Homes
In January of 2015, a company revealed a six-story home that they made with a 3D printer. The best to way to explain how a 3D printer works is to contrast it with a typical printer that uses ink to print on a sheet of paper. The thickness of the ink is so infinitesimally small that if you held the paper up to your face, you likely wouldn’t be able to see any elevation of ink on the printed area of the page.
Now imagine if the printer used a thicker type of ink and printed on that sheet of paper not just once, but in multiple layers over the same area. Eventually the inked area would become raised. If you used a different printing material other than ink, and you altered the printer’s instructions to achieve a certain height, you might eventually be able to print something like a plastic bowl. That’s how 3D printing works, and the options of materials and instructions you can use to print are only limited by your imagination.
3D printing is currently an explosive field where lots of entrepreneurs have trained their sights. Already, we have 3D printers that make toys, apparel, even car parts. How about 3D printing to make a home? The same company that used the 3D printer to make that six-story home in 2015 had a year earlier made 10 stand-alone one-story houses with a 3D printer from construction waste and cement.
Although, I must tell you that I wasn’t at all impressed by the video I saw of the 3D printed home on YouTube. The company that made these homes basically rigged a giant squirt gun to repeatedly squirt layer after layer of cement in a pattern that ended up forming the walls of each house. If 3D printing is going to revolutionize the construction industry, it certainly won’t happen with this implementation. Nonetheless, I wanted to speak to the inventor of this 3D printing technology to see how this technology might be used more effectively in the future.
Colonies On Mars And Machines In The Meteor Belt
Behrokh Khoshnevis is a professor of Industrial and Systems Engineering at the University of Southern California. He patented the Contour Crafting system that seems to have been sloppily implemented to 3D print the house in the YouTube video. Behrokh has no relationship with the company that built those homes.
If you really want to see the future of construction, you have to listen to how 3D printing would work in the most ideal circumstances. What I’m about to explore is out of this world. Literally. Behrokh is currently working with NASA to use 3D printers to build structures on Mars.
Behrokh Khoshnevis: “I approached NASA with a proposal to use lunar and Martian in situ material and build the structures. As opposed to all the proposed methods of taking stuff from here and building stuff on those planets, I recommended a much more viable approach. If there is a technology that can use what is up there, of course it would be economically much more attractive.”
Me: “So the extraterrestrial approach would be, you would transport the 3D printer, if you will, and the associated materials?”
This was a pretty stupid question. Prior to speaking with Behrokh, I hadn’t given any thought to the business of building structures on the Moon or Mars. But obviously, if you’re going to start construction there, and you want to build out of concrete, you wouldn’t bring the concrete from Earth. Concrete is made from sand or some type of gravel, water, and cement. So if it’s possible to get the sand or gravel from space, why carry it with you from our planet?
Behrokh Khoshnevis: “In situ materials. Use whatever is on the moon and whatever is on Mars and build with those. And I demonstrated that that can be done. We built pretty strong structures with the material that is up there. We made some kind of concrete without using water.”
Me: “That’s fasci...
If you like this episode you’ll love
Episode Comments
Generate a badge
Get a badge for your website that links back to this episode
<a href="https://goodpods.com/podcasts/predicting-our-future-53410/episode-4-nyc-goes-modular-2707900"> <img src="https://storage.googleapis.com/goodpods-images-bucket/badges/generic-badge-1.svg" alt="listen to episode 4: nyc goes modular on goodpods" style="width: 225px" /> </a>
Copy