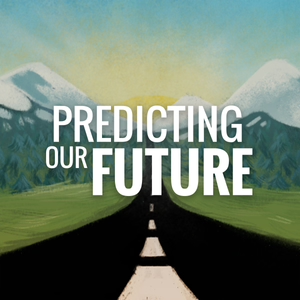
Episode 3: Google, China, & Overnight Cities
03/15/17 • 25 min
If a trillion dollar market opportunity exists, you can bet the people at Google are thinking about it. Within X, Google’s most secretive lab, they’ve been working on solving the problem of how to make building construction more efficient in order to deal with the world’s severe and worsening urban housing shortage. By the year 2050, the global population is expected to grow by 2.2 billion people, and 90% of that growth is expected to take place in cities that are in dire need of new housing. In China, one company has figured out how to deal with this challenge by prefabricating components for skyscrapers inside of a factory.
Sponsored by:
If you’re a startup, apply for DigitalOcean’s Hatch program, where if selected, you’ll have access to their cloud for 12 months, in addition to technical training and mentorship. You can also go to do.co/predictingourfuture and ask the sales team for a free trial.
Interviewees
Episode Excerpt
Google & Flux
When you hear the word Google, you first and foremost associate it with search. You have a disagreement with someone: let’s Google it. You want to know where to vacation: Google it. You want to know what a company does: Google it.
But if you’ve been watching Google over the years, you know that Google does much more, than well, Google. There’s Gmail and Google Hangouts and Google Apps and Google Drive. The relationship between these offshoots became so obvious that Google just decided to brand them collectively as the “G Suite.” Somewhere along Google’s path of phenomenal success, the company decided to start working on some super interesting and hard problems that are really unrelated to the company’s initial mission of organizing the world’s information. The founders of Google have become so invested in developing other businesses that the company is no longer called Google. In January of 2016, the company was renamed Alphabet, with Google becoming just one of their subsidiaries.
Calico is Alphabet’s biotech subsidiary that is focused on extending human life. Verily is Alphabet’s life sciences subsidiary. One of their projects is to develop contact lenses for diabetics that are able to determine when a person’s glucose levels are running high. And then there is Google X, now referred to simply as “X,” the secretive think tank within Alphabet pioneering projects like the driverless car that will one day make the act of driving obsolete.
On the website for X, the mission statement reads: “We’re a moonshot factory. Our mission is to invent and launch ‘moonshot’ technologies that we hope could someday make the world a radically better place.” Google can be very secretive about their work, and this is ground zero for where their secret projects are born. X’s stealth projects have one of three outcomes: they are elevated to a division within Google and made public, they are spun out to become a separate stand-alone company, or they are killed.
To date, the only company to ever come out of X and be spun out into a separate entity is Flux. I spoke with Jen Carlile, a Co-founder of Flux, who initially joined Google as a software engineer in 2010.
Jen Carlile: “The way that Google X works is they identify what they call ‘world scale problems’ and then put a group of smart people together and say, ‘try to come up with a solution for this that can be tackled within a 10 year time horizon.’ So our big hairy problem was urban population growth. And the Google X leadership recognized that the pace at which we’re building buildings and with the way that we do it now, we’re simply not going to be able to keep up with urban population growth.”
In 1803, just 3% of the world’s population resided in urban areas. I have this romantic image of living in the 18th century in a glamorous European city. But as it turns out, if you lived in a city in the early 1800’s, you were part of a minority. This was before the Industrial Revolution had caused massive migrations from the country to cities where factories were located. The result of these massive migrations? By 1900, 14% of the world’s population was living in cities. In 1950, the percentage of the world’s population that lived in cities was 30%. And then in 2008, for the first time in the history of the world, the percentage of people living in cities equaled the percentage of people who lived outside of cities.
Here’s where it gets interesting. As of 2016, there are 7.4 billion people on the planet. 2.2 billion people are expected to join us by the year 2050, and 90% of this growth is expected to take place in cities.
It’s really hard to make sense of what the...
If a trillion dollar market opportunity exists, you can bet the people at Google are thinking about it. Within X, Google’s most secretive lab, they’ve been working on solving the problem of how to make building construction more efficient in order to deal with the world’s severe and worsening urban housing shortage. By the year 2050, the global population is expected to grow by 2.2 billion people, and 90% of that growth is expected to take place in cities that are in dire need of new housing. In China, one company has figured out how to deal with this challenge by prefabricating components for skyscrapers inside of a factory.
Sponsored by:
If you’re a startup, apply for DigitalOcean’s Hatch program, where if selected, you’ll have access to their cloud for 12 months, in addition to technical training and mentorship. You can also go to do.co/predictingourfuture and ask the sales team for a free trial.
Interviewees
Episode Excerpt
Google & Flux
When you hear the word Google, you first and foremost associate it with search. You have a disagreement with someone: let’s Google it. You want to know where to vacation: Google it. You want to know what a company does: Google it.
But if you’ve been watching Google over the years, you know that Google does much more, than well, Google. There’s Gmail and Google Hangouts and Google Apps and Google Drive. The relationship between these offshoots became so obvious that Google just decided to brand them collectively as the “G Suite.” Somewhere along Google’s path of phenomenal success, the company decided to start working on some super interesting and hard problems that are really unrelated to the company’s initial mission of organizing the world’s information. The founders of Google have become so invested in developing other businesses that the company is no longer called Google. In January of 2016, the company was renamed Alphabet, with Google becoming just one of their subsidiaries.
Calico is Alphabet’s biotech subsidiary that is focused on extending human life. Verily is Alphabet’s life sciences subsidiary. One of their projects is to develop contact lenses for diabetics that are able to determine when a person’s glucose levels are running high. And then there is Google X, now referred to simply as “X,” the secretive think tank within Alphabet pioneering projects like the driverless car that will one day make the act of driving obsolete.
On the website for X, the mission statement reads: “We’re a moonshot factory. Our mission is to invent and launch ‘moonshot’ technologies that we hope could someday make the world a radically better place.” Google can be very secretive about their work, and this is ground zero for where their secret projects are born. X’s stealth projects have one of three outcomes: they are elevated to a division within Google and made public, they are spun out to become a separate stand-alone company, or they are killed.
To date, the only company to ever come out of X and be spun out into a separate entity is Flux. I spoke with Jen Carlile, a Co-founder of Flux, who initially joined Google as a software engineer in 2010.
Jen Carlile: “The way that Google X works is they identify what they call ‘world scale problems’ and then put a group of smart people together and say, ‘try to come up with a solution for this that can be tackled within a 10 year time horizon.’ So our big hairy problem was urban population growth. And the Google X leadership recognized that the pace at which we’re building buildings and with the way that we do it now, we’re simply not going to be able to keep up with urban population growth.”
In 1803, just 3% of the world’s population resided in urban areas. I have this romantic image of living in the 18th century in a glamorous European city. But as it turns out, if you lived in a city in the early 1800’s, you were part of a minority. This was before the Industrial Revolution had caused massive migrations from the country to cities where factories were located. The result of these massive migrations? By 1900, 14% of the world’s population was living in cities. In 1950, the percentage of the world’s population that lived in cities was 30%. And then in 2008, for the first time in the history of the world, the percentage of people living in cities equaled the percentage of people who lived outside of cities.
Here’s where it gets interesting. As of 2016, there are 7.4 billion people on the planet. 2.2 billion people are expected to join us by the year 2050, and 90% of this growth is expected to take place in cities.
It’s really hard to make sense of what the...
Previous Episode
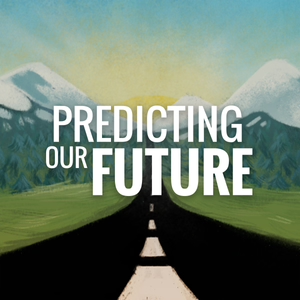
Episode 2: Half-priced Hamptons
Modern homebuilders have taken the art of prefabrication to new heights where they can construct entire rooms complete with insulation, plumbing, and electric wiring all within a factory. These rooms, called “modules,” are then transported from the factory to the building site and stacked to form a home in mere days. In the Hamptons, Seattle, San Francisco, Los Angeles, and a number of other major cities, it’s now possible to build a beautiful modern home modularly for dramatically less than the cost of building with local contractors.
Sponsored by:
If you’re a startup, apply for DigitalOcean’s Hatch program, where if selected, you’ll have access to their cloud for 12 months, in addition to technical training and mentorship. You can also go to do.co/predictingourfuture and ask the sales team for a free trial.
Interviewees
Episode Excerpt
Modular Homebuilding
When it comes to homes built in factories, people use the term “prefabricated” to mean a number of different things. In a history spanning hundreds of years, which I briefly covered in the last podcast episode, people have long assembled house components off-site and then shipped those components to sites along with instruction manuals for assembly. Prefabrication has been used for everything from sending houses from England to Australia via ship in the 1800’s to rapid construction of suburban home developments in post-World War II America.
In modern times, home pieces are precisely cut to size in a factory, so a finished building made primarily from these pieces can be accurately called “factory-built.” Once you’ve constructed all the pieces for the home, it’s usually a relatively straightforward proposition to ship them, as they’re designed to fit inside of a container that goes on the back of a flatbed truck. While this prefabricated kit-based approach to homebuilding can provide virtually unlimited flexibility in design, it can still take a while to assemble once the pieces arrive at the building site, especially if the construction crew doesn’t have experience building with that particular type of kit.
In the world of factory-built housing, the alternative to a kit build is a modular approach where a box, in the form of four walls, a floor, and a ceiling, also known as a “module,” is constructed inside of a factory and then shipped to the site. There are varying degrees of completion of these boxes in the factory. In some instances, the walls are complete and the plumbing and electrical wiring are already in the walls. These homes can go up in a matter of days, instead of weeks or months. Outside of the United States, this type of construction is called a “volumetric build.”
Bill Haney & Blu Homes
The most high-profile modular builder in America with venture backing is Blu Homes, the company I spoke with in the last episode that Forbes once described as “The Apple Of Green Prefab Homes.” At one point, Blu Homes was selling nationally, but the company found that it was necessary to work very closely with subcontractors in the field who could pour the foundation and set the home. Bill Haney, the Founder and CEO, made clear that the expansion of those relationships would be a slow and painstaking process.
Bill Haney: “In California, we’re building enough concentration at present that we know the local subcontractors who dig the foundation or put in the driveway or do the electrical hookups. And in the great state of New York, we know them in some places some of the time, and when we don’t know them, the customer or we get hurt. So we just feel like the right answer, the prudent answer, is to grow in stages, and the reality is that the great state of California is going to build 40,000 new houses this year.”
Building near your corporate headquarters has advantages, but with California in particular, there’s a sense that Bill is facing the toughest building code of any state in the country for green building standards. So his perspective was also a little bit of, “If I can build this right in California, I can make it work anywhere.”
I live in New York, so Blu Homes is not an option for me – at least not if I want to put up a home in the state of New York. To the best of my knowledge, there have been no East Coast venture firms rushing to fill the void by putting $200 million into an East Coast Blu Homes equivalent. But that hasn’t stopped other companies from trying to seize the modular home building opportunities available on the East Coast.
The Tipping Point
I started these interviews in search of a tipping point: some changed circumstance that would cause most peo...
Next Episode
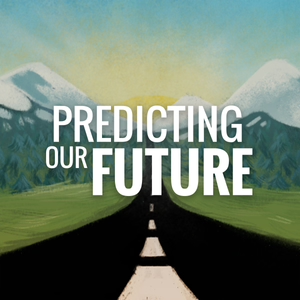
Episode 4: NYC Goes Modular
In the summer of 2016, the world’s tallest modular building at 32 stories high was completed at 461 Dean Street in Brooklyn, NY. Once the building’s apartment modules were completed at a factory located in the Brooklyn Navy Yard, they were transported to the development site and essentially stacked one on top of another into a high-rise building. To the dismay of its original backers, the building was delivered years late, riddled with construction problems, and the subject of a costly litigation. Still, excitement about modular construction in New York abounds with new projects under development.
Sponsored by:
If you’re a startup, apply for DigitalOcean’s Hatch program, where if selected, you’ll have access to their cloud for 12 months, in addition to technical training and mentorship. You can also go to do.co/predictingourfuture and ask the sales team for a free trial.
Interviewees
Episode Excerpt
U.S. Multi-Family Building
If you were paying any attention to the 2016 U.S. presidential election, you would think that just about every factory in the United States has either left for China or is about to leave. But when it comes to factories that are currently building apartments, or will soon be building apartments, we’re probably just getting started with constructing these factories in the United States.S hipping costs make transporting building modules from overseas to the United States expensive. And while one Polish company has managed to successfully transport modules here, the transportation expense is likely to make this a predominantly local industry. That, along with undeniable demographic shifts afoot in the United States that will be pushing the demand much higher for multi-family buildings in urban areas, suggest that we may very well witness the transformation of American factory-built construction into a multi-billion dollar industry.
Based on what world populations and growth rates suggest, you might think that the urgent need for urban housing over the next 30 years will largely be an African and Asian phenomenon. But the truth is that the migration to cities is also expected to happen right here at home. The United States Census Bureau provides statistics on the number of permits issued for new construction starts each year throughout the entire country. In 2015, 41% of permits were issued for structures that consisted of two or more units (referred to as a “multi-family residence”). Not exactly a screaming validation of my argument that you should be building modular multi-family buildings in cities when 59% of permits were for single-family residences.
But let’s look at the trend line towards multi-family construction over the past 25 years. Again, from the United States Census Bureau’s website:
- In 1991, 21% of permits were for multi-family residences;
- In 2000, 25% of permits were for multi-family residences;
- In 2007, 30% of permits were for multi-family residences;
- And again, in 2015, 41% of permits were for multi-family residences.
The rising trend of multi-family starts, as a percentage of total building starts, is unmistakeable. Here’s another interesting set of facts. The U.S. Census Bureau breaks down the multi-family residence into three categories: two units; three and four units; and five units and up:
In 1991, 79% of the multi-family category permits were for buildings with five plus units;
By 2015, 93% of permits in the multi-family category were for buildings with five plus units.
As it turns out, if you’re an entrepreneur and thinking about factory-built housing in the United States, the biggest market to go after today is single-family homes. But if the trend towards urban development continues, the biggest market to attack will soon be for multi-family homes. In New York City, two companies began with a modular approach, meaning they were building boxes inside of factories that would be stacked one on top of another once they arrived on the jobsite.
Brooklyn
New York City’s population is growing. In 2014, the city was home to just under 8.5 million people. By 2030, we’re expected to surpass 9 million people. In 2016 alone, New York City will add a total of 24,575 new apartments. My home in Brooklyn will lead all the other boroughs with over 6,000 new units.
At the end of this podcast series on factory-built housing, I’ll make some predictions about what the future will look like and who will be the winners in this space. Without giving it all away, I can tell you who I don’t expect to be the agents of massive change: billionaire New York real estate developers. And tha...
If you like this episode you’ll love
Episode Comments
Generate a badge
Get a badge for your website that links back to this episode
<a href="https://goodpods.com/podcasts/predicting-our-future-53410/episode-3-google-china-and-overnight-cities-2707913"> <img src="https://storage.googleapis.com/goodpods-images-bucket/badges/generic-badge-1.svg" alt="listen to episode 3: google, china, & overnight cities on goodpods" style="width: 225px" /> </a>
Copy