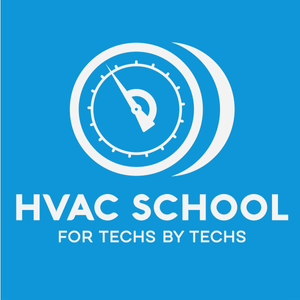
What is Standard 310? w/ Eric Kaiser & Chris Hughes
05/30/24 • 60 min
Standard 310 is a technical workflow created by ACCA, ResNet, and ANSI for grading the installation of HVAC systems, typically in new home construction. It plays a crucial role in obtaining Energy Star certification, which can qualify homeowners for tax credits under the Inflation Reduction Act. The five steps of Standard 310 are design review, duct leakage test, total system airflow, blower fan watt draw, and refrigerant charge verification.
In this podcast episode, host Bryan Orr is joined by guests Chris Hughes and Eric Kaiser to discuss Standard 310 and its implications for HVAC contractors.
The standard aims to ensure that HVAC systems are installed correctly and operate as designed. The process involves a third-party HERS rater conducting various tests and measurements, which contractors need to be prepared for. Proper duct sealing, airflow settings, and refrigerant charging are critical for passing the assessments.
One of the challenging aspects highlighted is the refrigerant charge verification step. The standard requires either non-invasive testing (which has temperature limitations) or weigh-in verification with geotagged photos. Chris Hughes suggests manufacturers could develop more consistent commissioning protocols to streamline this process.
Topics covered in the podcast:
- Overview of Standard 310 and its five steps
- Importance for Energy Star certification and tax credits
- Role of HERS raters and HVAC contractors
- Duct leakage testing and proper sealing
- Airflow measurement methods
- Blower fan watt draw challenges
- Refrigerant charge verification options
- Need for consistent commissioning protocols
- Coordination and documentation required
- Future improvements to the standard
Have a question that you want us to answer on the podcast? Submit your questions at https://www.speakpipe.com/hvacschool. Purchase your virtual tickets for the 5th Annual HVACR Training Symposium at https://hvacrschool.com/Symposium24. Subscribe to our podcast on your iPhone or Android. Subscribe to our YouTube channel. Check out our handy calculators here or on the HVAC School Mobile App for Apple and Android.
Standard 310 is a technical workflow created by ACCA, ResNet, and ANSI for grading the installation of HVAC systems, typically in new home construction. It plays a crucial role in obtaining Energy Star certification, which can qualify homeowners for tax credits under the Inflation Reduction Act. The five steps of Standard 310 are design review, duct leakage test, total system airflow, blower fan watt draw, and refrigerant charge verification.
In this podcast episode, host Bryan Orr is joined by guests Chris Hughes and Eric Kaiser to discuss Standard 310 and its implications for HVAC contractors.
The standard aims to ensure that HVAC systems are installed correctly and operate as designed. The process involves a third-party HERS rater conducting various tests and measurements, which contractors need to be prepared for. Proper duct sealing, airflow settings, and refrigerant charging are critical for passing the assessments.
One of the challenging aspects highlighted is the refrigerant charge verification step. The standard requires either non-invasive testing (which has temperature limitations) or weigh-in verification with geotagged photos. Chris Hughes suggests manufacturers could develop more consistent commissioning protocols to streamline this process.
Topics covered in the podcast:
- Overview of Standard 310 and its five steps
- Importance for Energy Star certification and tax credits
- Role of HERS raters and HVAC contractors
- Duct leakage testing and proper sealing
- Airflow measurement methods
- Blower fan watt draw challenges
- Refrigerant charge verification options
- Need for consistent commissioning protocols
- Coordination and documentation required
- Future improvements to the standard
Have a question that you want us to answer on the podcast? Submit your questions at https://www.speakpipe.com/hvacschool. Purchase your virtual tickets for the 5th Annual HVACR Training Symposium at https://hvacrschool.com/Symposium24. Subscribe to our podcast on your iPhone or Android. Subscribe to our YouTube channel. Check out our handy calculators here or on the HVAC School Mobile App for Apple and Android.
Previous Episode
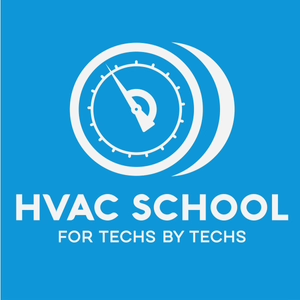
Q&A - Kitchen Exhaust and Makeup Air - Short #197
In this short Q&A podcast episode, Bryan answers Gunther's question about kitchen exhaust and makeup air. Gunther asked if there were any studies that showed that makeup air should come very close to the hood to avoid infiltration. He also asked how to educate others who push back against the idea, particularly in kitchen exhaust systems of around 600 CFM.
Commercial facilities, especially restaurants, bring in makeup air to balance out the air being exhausted. There are costs associated with makeup air, but there are plenty of valid reasons to add it to residential structures. Being able to control the makeup air allows us to control where we bring air in from (especially when it comes to drawing in humid air or dirty attic air from gaps and cracks, particularly in vented attics).
Open-combustion appliances in the building envelope are also prone to backdrafting if the structure is under negative pressure. The structure is also more likely to have its dryer vents experience leaks under negative pressure.
The International Residential Code (IRC) (section M1503.6.2) requires makeup air when you have an exhaust system >400 CFM. The Florida Residential Code (section M1503.4) requires kitchen exhaust systems exceeding 400 CFM to have makeup air at approximately the same rate as the exhaust rate. Furthermore, the Florida Mechanical Code (section 505.2) specifies that kitchen exhaust systems exceeding 400 CFM must have makeup air to balance the air pressure and ensure proper ventilation.
Have a question that you want us to answer on the podcast? Submit your questions at https://www.speakpipe.com/hvacschool. Purchase your virtual tickets for the 5th Annual HVACR Training Symposium at https://hvacrschool.com/Symposium24. Subscribe to our podcast on your iPhone or Android. Subscribe to our YouTube channel. Check out our handy calculators here or on the HVAC School Mobile App for Apple and Android.
Next Episode
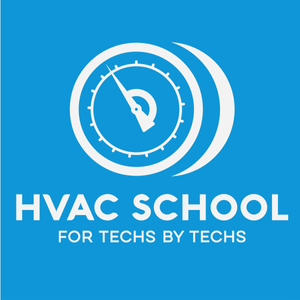
Rack Refrigeration Class Part 1
This podcast episode is Part 1 of a Kalos class on rack refrigeration given by Matthew Taylor. This first segment focuses on the basic refrigerant circuit and oil management of a parallel rack system, common in market refrigeration.
Parallel racks follow the same general process as any other compression refrigeration system. However, they contain multiple compressors on a single rack. These systems have multiple suction lines that tie into one single suction header that feeds into multiple compressors. The suction side of the piping is usually a long distance with varying elevations; risers are vertical stretches of piping that carry oil and refrigerant up and pose a challenge for oil return.
The compressor takes low-pressure vapor on the suction side and turns it into high-pressure vapor on the discharge side. From there, the condenser rejects heat from the refrigerant, which brings the superheated vapor down to saturation temperature and further rejects heat to make the refrigerant fully liquid (subcooled). Metering devices drop the pressure of the refrigerant, and the cases contain evaporators that absorb heat and boil off refrigerant, which travels to the compressors via the suction lines.
Parallel racks come in multiple varieties, but the ones in this podcast are of the direct expansion (DX) variety. Saturation remains a critical principle in these systems: superheat, subcooling, and the pressure-temperature relationship all drive system operation.
Matthew also covers:
- Different types of rack refrigeration systems
- Customized variations between racks
- Looking up case information and reading legends
- Oil return and controlling velocity
- Mechanical subcooling
- Full load amps (FLA) and locked rotor amps (LRA)
- Temperature glide: dew point, bubble point, and midpoint
- EPR installation
- Evaporator efficiency and superheat
- Compressor types
- Compression ratio and liquid or vapor injection
- Oil management components and controls
Have a question that you want us to answer on the podcast? Submit your questions at https://www.speakpipe.com/hvacschool. Purchase your virtual tickets for the 5th Annual HVACR Training Symposium at https://hvacrschool.com/Symposium24. Subscribe to our podcast on your iPhone or Android. Subscribe to our YouTube channel. Check out our handy calculators here or on the HVAC School Mobile App for Apple and Android.
If you like this episode you’ll love
Episode Comments
Generate a badge
Get a badge for your website that links back to this episode
<a href="https://goodpods.com/podcasts/hvac-school-for-techs-by-techs-60475/what-is-standard-310-w-eric-kaiser-and-chris-hughes-52926404"> <img src="https://storage.googleapis.com/goodpods-images-bucket/badges/generic-badge-1.svg" alt="listen to what is standard 310? w/ eric kaiser & chris hughes on goodpods" style="width: 225px" /> </a>
Copy