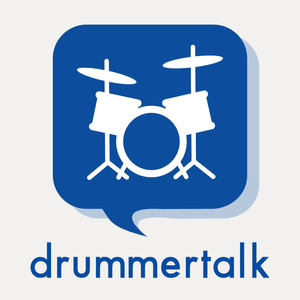
Drummer Talk 254 – Drum Kit Makeover Part 3: Refinishing
05/28/15 • 98 min
We dive into refinishing on part 3 of our series on drum kit makeovers!!
Opening Detritus
Drummer Talk Mailbag
From Rich:
Thank you Dave and Troy!
I’m totally geeking out on the refinishing series. I’ve been contemplating building an exotic wood kit from Keller shells so can’t wait for the show on veneering. Recovering my current (cheap Guitar Center Sound Percussion) kit, however, may be more realistic. I’ve replaced everything but the hardware, tung oiled the interior, and cleaned up the bearing edges. While not as punchy as I would like, my drum teacher is amazed at the sound quality. Dave jokes about Wal-mart contact paper, but before these shows I actually considered putting 3M carbon fiber automotive vinyl over the existing wrap. After listening to the re-wrapping show, I found that Bum Wrap Drum Company has some beautiful exotic wood wraps. Re-wrapping my current kit would certainly be easier than veneering new shells, but I don’t think I could ever get over the psychological hurdle of knowing that I’m playing crappy shells. I’d love your thoughts.
Rich
From Chris:
Dave and Troy, I love the podcast. It helps get me through the work week. In the past, Troy has mentioned music companies are always looking for technology specialists. Can you touch on ways to seek out these opportunities and maybe list off top music companies that are out there? From what I have seen, many companies are held by larger organizations and jobs may be posted under a different company than expected. I’d love to do something involving music, but have not been able to find anything in the Missouri area. Any ideas? Thanks! Chris
From Dan:
Greetings gentlemen. First off, if this podcast ever went off the air there’d be a void in my life that would, sadly, remain unfulfilled. So, do me (and drummers worldwide) the favour of keeping on doing what you’re doing! OK, enough butt-kissing... I just finished listening to and thoroughly enjoying episode 252. One thing that made me go “what the heck...” was the comment about how Ludwig replacement parts are so ubiquitous. This may be true with the exception of the P-85 strainer. I’ve called/emailed every drum part company I can find and no one makes a 2.5′′ hole spaced aftermarket strainer. All of the P-85 style options won’t fit Ludwig’s spacing. I have an LM402 and an Acrolite and it drives me nuts that it’s not drum key operable. When you said they’ve been using this design for 60 years I believe it. If they would only get with the program every other drum company figured out 30+ years ago I (and many others) quit b****ing about it. I love Ludwig snares, but for the price they charge it’s frankly idiotic that they continue to use Phillips head screws instead of drum key screws. Rant over, thanks for reading.
News
Topic Notes
Places To buy Materials
- 220 and 320 grit sand paper
- Flexible Sanding Sponge or –3M Stikit 6′′ Disc Hand Pad
- Transtint Dyes
- Cheap Sponge Applicator
- Water or Denatured Alcohol
- 3M Blue Painters Tape LOW ADHESIVE
- #0000 Steel Wool
- Tung Oil ...
We dive into refinishing on part 3 of our series on drum kit makeovers!!
Opening Detritus
Drummer Talk Mailbag
From Rich:
Thank you Dave and Troy!
I’m totally geeking out on the refinishing series. I’ve been contemplating building an exotic wood kit from Keller shells so can’t wait for the show on veneering. Recovering my current (cheap Guitar Center Sound Percussion) kit, however, may be more realistic. I’ve replaced everything but the hardware, tung oiled the interior, and cleaned up the bearing edges. While not as punchy as I would like, my drum teacher is amazed at the sound quality. Dave jokes about Wal-mart contact paper, but before these shows I actually considered putting 3M carbon fiber automotive vinyl over the existing wrap. After listening to the re-wrapping show, I found that Bum Wrap Drum Company has some beautiful exotic wood wraps. Re-wrapping my current kit would certainly be easier than veneering new shells, but I don’t think I could ever get over the psychological hurdle of knowing that I’m playing crappy shells. I’d love your thoughts.
Rich
From Chris:
Dave and Troy, I love the podcast. It helps get me through the work week. In the past, Troy has mentioned music companies are always looking for technology specialists. Can you touch on ways to seek out these opportunities and maybe list off top music companies that are out there? From what I have seen, many companies are held by larger organizations and jobs may be posted under a different company than expected. I’d love to do something involving music, but have not been able to find anything in the Missouri area. Any ideas? Thanks! Chris
From Dan:
Greetings gentlemen. First off, if this podcast ever went off the air there’d be a void in my life that would, sadly, remain unfulfilled. So, do me (and drummers worldwide) the favour of keeping on doing what you’re doing! OK, enough butt-kissing... I just finished listening to and thoroughly enjoying episode 252. One thing that made me go “what the heck...” was the comment about how Ludwig replacement parts are so ubiquitous. This may be true with the exception of the P-85 strainer. I’ve called/emailed every drum part company I can find and no one makes a 2.5′′ hole spaced aftermarket strainer. All of the P-85 style options won’t fit Ludwig’s spacing. I have an LM402 and an Acrolite and it drives me nuts that it’s not drum key operable. When you said they’ve been using this design for 60 years I believe it. If they would only get with the program every other drum company figured out 30+ years ago I (and many others) quit b****ing about it. I love Ludwig snares, but for the price they charge it’s frankly idiotic that they continue to use Phillips head screws instead of drum key screws. Rant over, thanks for reading.
News
Topic Notes
Places To buy Materials
- 220 and 320 grit sand paper
- Flexible Sanding Sponge or –3M Stikit 6′′ Disc Hand Pad
- Transtint Dyes
- Cheap Sponge Applicator
- Water or Denatured Alcohol
- 3M Blue Painters Tape LOW ADHESIVE
- #0000 Steel Wool
- Tung Oil ...
Next Episode
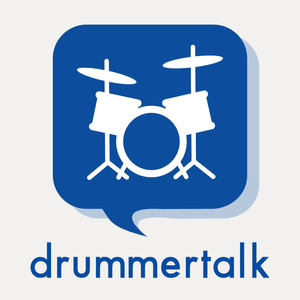
Drummer Talk 255 – Drum Kit Makeover Part 4: Veneers
We wrap up our multi-part series on drum kit makeovers today by talking about veneers!
Opening Detritus
- It’s the mid-season finale. We’ll be revisiting website features like reviews and transcriptions during the summer!
Drummer Talk Mailbag
From Sebastian
I’m listening to your podcast over here in Germany. You guys really make my day on the way to work every morning. Thanks for keeping me inspired.
When you said you were spending the whole weekend on improving your mixing and mastering skills I thought: Holy Cow! One weekend for mixing AND mastering is like trying to repaint the Empire State Building AND the Rockefeller Center in two days... with a toothbrush.
So apart from drumming I’m also into recording, mixing and well, maybe a bit of mastering. I’m not a professional but I know how frustrating all that DAW-business (compressors, reverbs, headroom, panning, EQing aso) can be.
I discovered another great podcast that covers a lot of your problems with recording, mixing, producing, composing and mastering. It was very useful for me and I believe it might also be helpful for you. So I would like to share Kenal Osborne’s Recording Lounge Podcast for those interested in the topics mentioned above.
Here is the link to the podcasts on Itunes. It is free.
Kendal has done several shows that could be interesting for drummers. I recommend Episodes: 13,14 ,22, 24, 25, 26, 27, 46, 49, 50 and 51
I absolutely love the idea of making a drummertalk show about composing, producing, mixing and mastering. Maybe you could even contact Kendal and make an interview with him, because I think he has some great knowledge on this subject.
Enjoy your summer break!
PS @Dave: I also have a Tama Starclassic Performer Set.
From Dan
OK, I promise this will be my last comment (rant) on the Ludwig P-85 strainer.
Last week when you read my comment you kinda deviated from the its core message. I, like many, don’t feel that Ludwig needs to deviate from the core look/feel of their strainer. If they would only make it drum key operable instead of phillips screwdriver they would alleviate a major pet peeve. By all means, they can keep the classic look and feel but give us drummers (who shell out a premium for their great sounding shells) a small bit of modernity.
Keep up the great work guys – your podcasts are “must listens”.
Cheers, Dan
News
- Dave Lombardo to Showcase Art Collection
- Drummer Takes Pride in Hitting Like a Girl
- Ginger Baker to Speak Out in New BBC series
Topic Notes – Veneers
Places To buy Materials
If you like this episode you’ll love
Episode Comments
Generate a badge
Get a badge for your website that links back to this episode
<a href="https://goodpods.com/podcasts/drummer-talk-481086/drummer-talk-254-drum-kit-makeover-part-3-refinishing-64378115"> <img src="https://storage.googleapis.com/goodpods-images-bucket/badges/generic-badge-1.svg" alt="listen to drummer talk 254 – drum kit makeover part 3: refinishing on goodpods" style="width: 225px" /> </a>
Copy