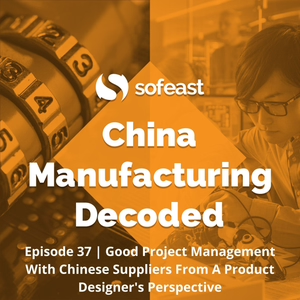
Andy Bartlett | Good Project Management With Chinese Suppliers From A Product Designer's Perspective
01/22/21 • 38 min
Adrian catches up with Andy Bartlett, an experienced British product designer who has 25 years of experience in product design, development, and working with manufacturers in China to discuss project management best practices when dealing with Chinese suppliers with a special focus on Andy's take on this from a product design perspective. He covers project management tips and techniques, building good relationships, IP protection, and much, much more!
More about Andy Bartlett
Andy has a deep experience in consumer electronics, toys, and more. Several of Sofeast's clients have worked with Andy with good results. He was Product Design Manager at Worlds Apart for 14 years and has designed products for Disney, LEGO, Hasbro and Mattel including Scruff-a-luvs and GoGlow.
Show Notes00:00 - Introducing the episode
01:23 - Andy's Bio
02:05 - The 2 ways of engaging with Chinese suppliers: Contract Manufacturers (your 'factory') and Development Houses - When you're developing a new product to bring to market you're likely to work directly with a factory in China and you'll need to go through all of the product development work that has been done and make sure they can deliver, or, if you're at an earlier stage on your project, you may work with a development house first who help you with the development work such as on the product concept and its functions and on NPI work such as deciding on manufacturing processes, techniques, and more.
03:36 - Dealing directly with a factory as a designer when performing the project management - 2 challenges: 1. Protect your interests (design intent) and be clear about what you want to achieve. 2. Structure, organisation, and well-controlled communication channels.
06:22 - Dealing with a development house from a design perspective - about managing costs, schedule and exploring opportunities (which they will be more interested in than many factories who are incentivised to get to production ASAP), but still getting to the factory in time to produce your goods on schedule.
07:55 - The focus on getting to production by factories and why creative people sometimes don't know when to stop 'development.'
09:10 - At what point do you know that your product development is mature enough that you can start production?
12:14 - Why approving the tooling is one of the worst times in the NPD process for anyone who's developing a new product.
13:26 - Exploring some best practices when working with a factory or a development house (good for hardware startups who are new to this). New product development is a tough process, so building a good working relationship is really helpful. Look for good communication and contacts whom you can trust (in factories this can be harder) and an inquisitive spirit that is willing to try new things and solve problems.
17:38 - How communication and building relationships have been affected by the challenges of the pandemic. In-person contact is the best way to work with your Chinese suppliers, but in lieu of that, video conferencing is a key tool.
19:47 - The culture of saying 'yes' to everything you request in China and how to combat it with notes and a system to check that suppliers are on target. Importers need to be careful of this, as yes doesn't always mean yes. Therefore any meetings should be followed up with written notes that can double-confirm a supplier's intent and ability. Google suite of products doesn't work in China, but you can create a system to track and manage development issues. Microsoft's software is usually adequate for this. Emails aren't as they're quite ignorable. Build the culture of 'track & trace' and always come back to suppliers to check that they are resolving your question and if it's truly a 'yes,' or in fact a 'no.'
24:44 - How best to manage CAD data and not lose the integrity of the modelling. A flexible pause and review approach to 3D data is a good use of time as this will be worked on until late in the development process.
27:09 - How about IP protection? It's context-driven. If you're in a long-term stable relationship with a supplier you should already have the trust that they use IP responsibly. With a new supplier, do they take steps to protect their other clients' confidentiality seriously if you're visiting their factory to tour it? If so, that's a good sign. If a trusted supplier recommends another supplier this may be a good sign. You should take steps to control CAD data by using software to minimize the amount of data the new supplier can see at an early stage.
30:57 - Why keeping your cool, even when things go wrong, is really important. Main...
Adrian catches up with Andy Bartlett, an experienced British product designer who has 25 years of experience in product design, development, and working with manufacturers in China to discuss project management best practices when dealing with Chinese suppliers with a special focus on Andy's take on this from a product design perspective. He covers project management tips and techniques, building good relationships, IP protection, and much, much more!
More about Andy Bartlett
Andy has a deep experience in consumer electronics, toys, and more. Several of Sofeast's clients have worked with Andy with good results. He was Product Design Manager at Worlds Apart for 14 years and has designed products for Disney, LEGO, Hasbro and Mattel including Scruff-a-luvs and GoGlow.
Show Notes00:00 - Introducing the episode
01:23 - Andy's Bio
02:05 - The 2 ways of engaging with Chinese suppliers: Contract Manufacturers (your 'factory') and Development Houses - When you're developing a new product to bring to market you're likely to work directly with a factory in China and you'll need to go through all of the product development work that has been done and make sure they can deliver, or, if you're at an earlier stage on your project, you may work with a development house first who help you with the development work such as on the product concept and its functions and on NPI work such as deciding on manufacturing processes, techniques, and more.
03:36 - Dealing directly with a factory as a designer when performing the project management - 2 challenges: 1. Protect your interests (design intent) and be clear about what you want to achieve. 2. Structure, organisation, and well-controlled communication channels.
06:22 - Dealing with a development house from a design perspective - about managing costs, schedule and exploring opportunities (which they will be more interested in than many factories who are incentivised to get to production ASAP), but still getting to the factory in time to produce your goods on schedule.
07:55 - The focus on getting to production by factories and why creative people sometimes don't know when to stop 'development.'
09:10 - At what point do you know that your product development is mature enough that you can start production?
12:14 - Why approving the tooling is one of the worst times in the NPD process for anyone who's developing a new product.
13:26 - Exploring some best practices when working with a factory or a development house (good for hardware startups who are new to this). New product development is a tough process, so building a good working relationship is really helpful. Look for good communication and contacts whom you can trust (in factories this can be harder) and an inquisitive spirit that is willing to try new things and solve problems.
17:38 - How communication and building relationships have been affected by the challenges of the pandemic. In-person contact is the best way to work with your Chinese suppliers, but in lieu of that, video conferencing is a key tool.
19:47 - The culture of saying 'yes' to everything you request in China and how to combat it with notes and a system to check that suppliers are on target. Importers need to be careful of this, as yes doesn't always mean yes. Therefore any meetings should be followed up with written notes that can double-confirm a supplier's intent and ability. Google suite of products doesn't work in China, but you can create a system to track and manage development issues. Microsoft's software is usually adequate for this. Emails aren't as they're quite ignorable. Build the culture of 'track & trace' and always come back to suppliers to check that they are resolving your question and if it's truly a 'yes,' or in fact a 'no.'
24:44 - How best to manage CAD data and not lose the integrity of the modelling. A flexible pause and review approach to 3D data is a good use of time as this will be worked on until late in the development process.
27:09 - How about IP protection? It's context-driven. If you're in a long-term stable relationship with a supplier you should already have the trust that they use IP responsibly. With a new supplier, do they take steps to protect their other clients' confidentiality seriously if you're visiting their factory to tour it? If so, that's a good sign. If a trusted supplier recommends another supplier this may be a good sign. You should take steps to control CAD data by using software to minimize the amount of data the new supplier can see at an early stage.
30:57 - Why keeping your cool, even when things go wrong, is really important. Main...
Previous Episode
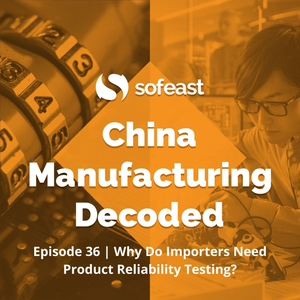
Why Do Importers Need Product Reliability Testing?
In This Episode...
Adrian and Renaud discuss the topic of product reliability testing. What is this type of testing, when do we carry it out, what are the risks of not doing the testing, and what does it cost? These questions and many more are answered, because today, more than ever, it's so important for importers to protect themselves against expensive recalls and lawsuits which may occur if your products don't reach expected reliability, quality, and, as a knock-on effect in many cases, safety standards.
Ultimately, you'll discover why, for most products, skipping reliability testing during the NPI process is simply not worth it!
Show Notes00:00 - Introduction
02:37 - A summary of WHAT product reliability is. Some examples are given, in particular, that of a women's razor that must be able to withstand the bathroom and shower environment and also a smartphone which needs to withstand daily use.
05:19 - If a product is NOT reliable, how could this affect the importer? You will face returns, bad reviews, and in the case of failures that lead to safety issues, you may have to recall a batch, be prosecuted in court, pay heavy damages, etc.
06:36 - What typically causes reliability issues in a new product? The causes of reliability issues can be broken down into categories:
- Design: Poor design is usually the top cause of reliability problems later on. The infamous case of the unsafe Samsung Galaxy Note 7 was down to a poor design that allowed the batteries to catch fire in certain circumstances.
- Manufacturing: Component manufacturers or manufacturing at the main assembly site can also cause reliability issues. An example is given of specifying the wrong kind of glue that later causes product failure (specifying the wrong materials or components is a type of design failure, too).
13:00 - Why product reliability is ever more important in these days of the internet when disgruntled users will soon write bad reviews. There is no one product category where users wouldn't complain about an unreliable product. Products for children would be an obvious target where brands can't afford to upset consumers, but on the other hand, something as simple as a takeaway coffee cup could also injure and upset consumers, too.
14:31 - The importance of understanding safety standards when developing a new product and planning ahead for any and all possible failures that could affect consumers.
15:41 - Will hardware startups, who may be new to reliability testing, get any support to define and plan for potential product failures from 3rd party companies (like Sofeast) who conduct the testing for them? Yes, although the developer really needs to understand their own users and how they may misuse the product better than anyone else. We will usually discuss the relevant regulations and potential risks with a customer who is developing a new product where needed, challenge their design and prototypes to assure that they're going in the right direction for their goals for the product, and we also often perform risk analysis and a design FMEA, too.
17:56 - How to confirm the performance of the product during development.
18:52 - How to push the limits of the product to work towards reliability during development. Some ideas of what to test to simulate the extremes that the product can be pushed to in order to see what fails first. This often uncovers the main weaknesses of a product's design.
20:56 - Reliability and compliance testing during mass production. Samples from the pilot run can be used to confirm that everything is OK with the product design, but also, importantly, the manufacturing process by subjecting them to typical usage over, say, 2 years. Compliance testing should also be done on these early pre-production pilot run samples, too.
24:19 - Why some companies still take the risk of not performing reliability testing. Those with less experience tend to place a lot of trust in their manufacturer, assuming that they will not provide products which later turn out to have reliability issues.
25:43 - The types of reliability testing that may be used. These vary per the product type, but here are some options:
- Cycling the product from low to high temperature, humidity testing, salt spray testing on exposed metals, mechanical tests like drop and vibration tests, flexing cables, lifecycle testing (HALT), and more.
- Packaging reliability testing is also a consideration, as it is often a part of the product offering ...
Next Episode
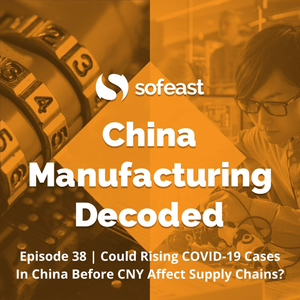
Could Rising COVID-19 Cases In China Before CNY '21 Affect Supply Chains?
In This Episode...
Adrian and Renaud discuss the rising number of COVID-19 cases in China barely a week or so before the Chinese New Year holiday is set to happen where tens of millions of people will travel home around the country.
The outbreak is centered on the North of the country at present, but if it were to spread this could lead to lockdowns throughout the country and the authorities are already raising alertness and preparations to suppress its spread as much as possible.
If you have a supply chain in China it's important to understand how this may affect the holiday, Chinese workers travelling around the country, and your suppliers.
Let's hear what's happening from China directly...
Show Notes00:00 - Introducing the episode
02:55 - What's the situation with coronavirus in China right now (Jan 28th 2021) and how may it affect manufacturing? Explaining the logistics of tens of millions of people moving around the country during this period. Why the government doesn't want a repeat of the Hubei lockdown.
09:20 - How large family meals and meeting other large households during CNY increases the risks.
10:58 - Could restrictions be more centered around the North of China, or more widespread? There are low, medium, and high-risk areas. Local governments have told companies to try to limit employees travelling home at all and requested stricter adherence to rules, such as mask-wearing. Government employees have been barred from travelling, but private company employees can travel.
14:03 - How tighter travel restrictions have caused perverse effects on the manufacturing industry in China earlier than usual. Knowing that travel will become more difficult and there may be quarantine periods (away from the family) for inter-province travellers, some staff have left to go home for CNY earlier than ever. In the case of key workers, such as machine specialists, this has affected factory productivity and output if there is no one else there who can do their jobs. So some factories have been forced to stop certain work 2 to 3 weeks earlier than usual.
17:53 - Why a lot of Chinese exporters are suffering, despite the 'boom' in exports. The unfavorable exchange rate is not helping companies who export from China, nor is the crazy logistics situation.
19:10 - If many workers don't travel home for CNY and opt to stay in the cities where they work, could this mean that factories get back to work sooner than usual after the holiday? It could be the case, especially in purely assembly or packing facilities which can operate of key people are not present. One problem could be that quality inspectors haven't gone back to work yet, though, which could lead to poorer quality products after CNY than usual.
20:44 - What's the worst-case scenario for importers with a Chinese supply chain? If very strict preventive measures are taken it could put a lot of workers in quarantine upon arrival back to their company's city from their hometown. If areas or provinces are locked down, this could affect your supply from companies in those areas (this happened with Hubei in 2020).
24:08 - A breakdown of some of the restrictions in place (based on info from Sofeast's HR manager in Guangdong). People who travel will need to show a negative test within a week of travelling and on return from some areas will have a mandatory 14 days of health monitoring at home. Restrictions could be stricter for medium/high-risk regions, for instance requiring a negative test within just a few days of travelling and, potentially, quarantining outside of home. The situation is changing every day, so by the time CNY occurs restrictions could be different again.
25:57 - Have any of Sofeast's staff decided not to travel? Yes, although others are waiting until closer to the time to see what happens with restrictions before making a final decision.
27:03 - Key points for importers to focus on during this time. Keep an eye on your suppliers, especially if they're in an area which is moved into medium/high-risk. Also consider sub-suppliers, as if they are locked down it could disrupt your suppliers' ability to fulfil your orders regardless of whether they're at work or not.
27:50 - The situation in Hong Kong. Given that some importers may have suppliers in Hong Kong, too, or wish to travel there, the situation has also recently become complicated due to a couple of localized outbreaks in Kowloon. HK has changed its approach to follow Mainland China more closely, now enforcing 3 weeks of quarantine in a hotel. Visitors can still travel to Hong Kong, unlike China which is only permitting a very limit...
If you like this episode you’ll love
Episode Comments
Generate a badge
Get a badge for your website that links back to this episode
<a href="https://goodpods.com/podcasts/china-manufacturing-decoded-50238/andy-bartlett-good-project-management-with-chinese-suppliers-from-a-pr-11264013"> <img src="https://storage.googleapis.com/goodpods-images-bucket/badges/generic-badge-1.svg" alt="listen to andy bartlett | good project management with chinese suppliers from a product designer's perspective on goodpods" style="width: 225px" /> </a>
Copy