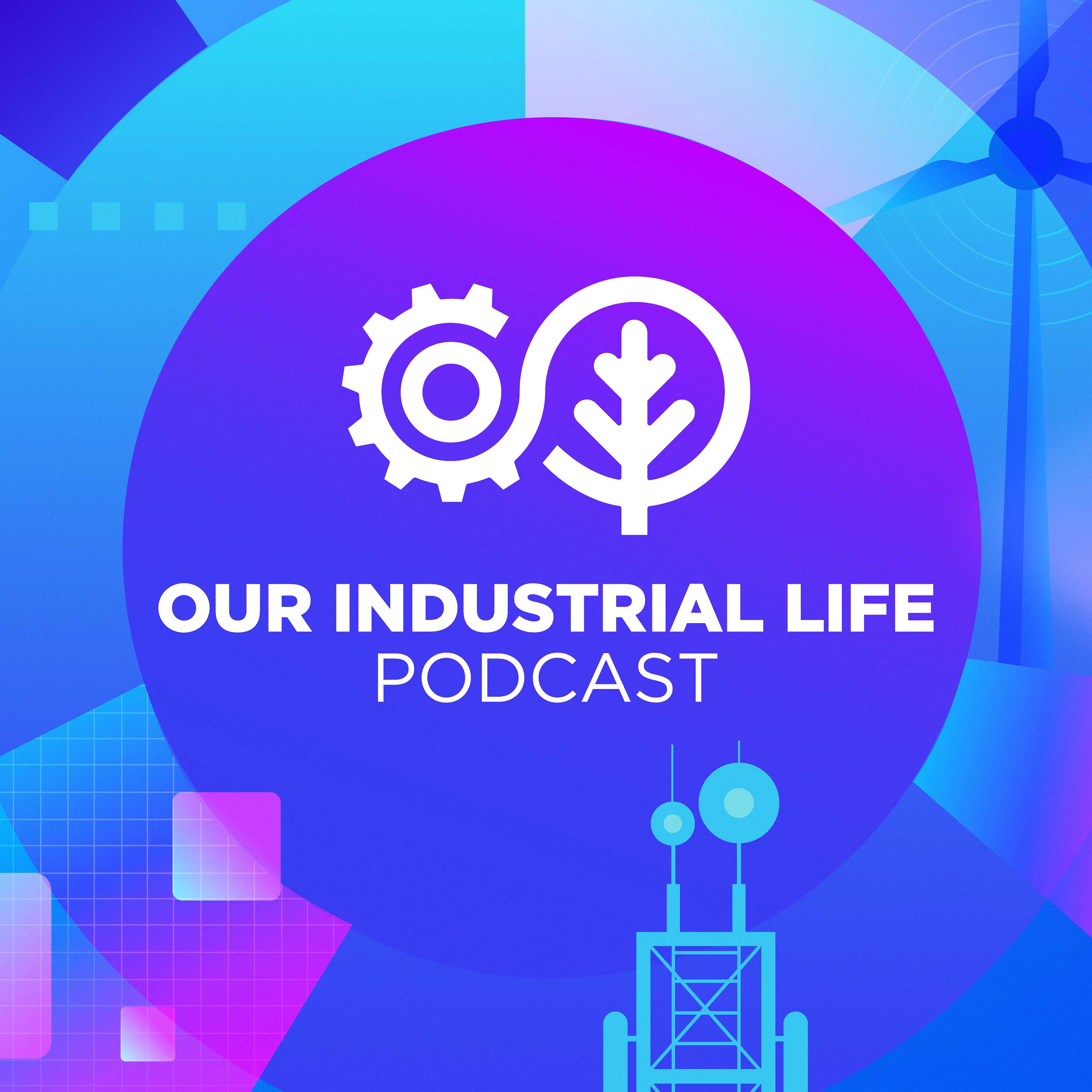
Digitization of sensor-based data to reach Cement 4.0
03/24/21 • 44 min
Guests: Berkan Fidan, Performance and Process Director, Oyak Cement
Martin Provencher, Mining Metals and Materials Industry Principal, AVEVA
Berkan Fidan describes a team approach to improving cement operations with sensor-based data. He started a 2016 digitalization project at Oyak Cement in Turkey, which leads Europe in cement production. As the performance and process director of his nation's largest cement producer he was trying to address the realities of cement production: enormous energy and heat costs and a product that sells for less than bottled water. He created a team consisting of production personnel from 7 cement plants and 3 grinding plants around the world and implemented a data collection and visualization system they referred to as Cement 4.0. Fidan reports his team did 90% of the work themselves. Among their accomplishments are 1) creating digital twins of their plants in Analysis Framework where they used a template of a kiln ID fan they created themselves to enforce common benchmarks and visualizations across their entire organization, 2) defining conditions for email notifications to local and corporate stakeholders of cement rotary kiln stoppage, and 3) creating event frames definitions to track and analyze mean time between failure.
By engaging local production personnel who found the system easy to use and popular, the system has seen organization-wide adoption and he attributes a clear improvement in KW per ton to the cultural change that has resulted.
Visit us at ourindustriallife.com
Guests: Berkan Fidan, Performance and Process Director, Oyak Cement
Martin Provencher, Mining Metals and Materials Industry Principal, AVEVA
Berkan Fidan describes a team approach to improving cement operations with sensor-based data. He started a 2016 digitalization project at Oyak Cement in Turkey, which leads Europe in cement production. As the performance and process director of his nation's largest cement producer he was trying to address the realities of cement production: enormous energy and heat costs and a product that sells for less than bottled water. He created a team consisting of production personnel from 7 cement plants and 3 grinding plants around the world and implemented a data collection and visualization system they referred to as Cement 4.0. Fidan reports his team did 90% of the work themselves. Among their accomplishments are 1) creating digital twins of their plants in Analysis Framework where they used a template of a kiln ID fan they created themselves to enforce common benchmarks and visualizations across their entire organization, 2) defining conditions for email notifications to local and corporate stakeholders of cement rotary kiln stoppage, and 3) creating event frames definitions to track and analyze mean time between failure.
By engaging local production personnel who found the system easy to use and popular, the system has seen organization-wide adoption and he attributes a clear improvement in KW per ton to the cultural change that has resulted.
Visit us at ourindustriallife.com
Previous Episode
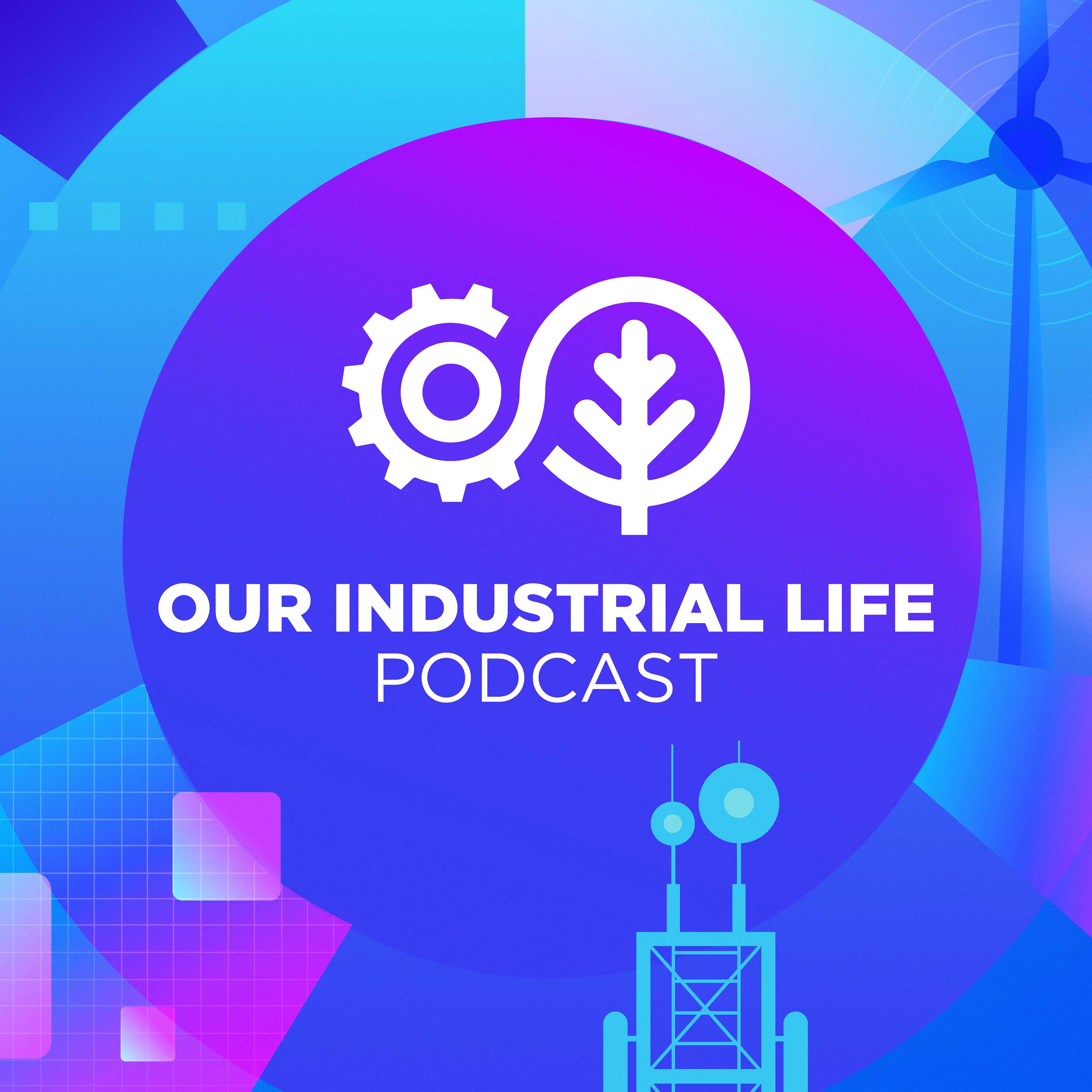
A hosted cloud solution for remote monitoring of indoor air quality.
Guests: Michael Orcutt, Vice President of Sales and Engineering, CosaTron
Richard Klein, Senior Product Marketing Manager, OSIsoft
Daniel Noonen, Partner Solution Architect
A manufacturer of advanced air purification systems can now monitor and provide analysis of indoor air quality remotely.
Visit us at ourindustriallife.com
Next Episode
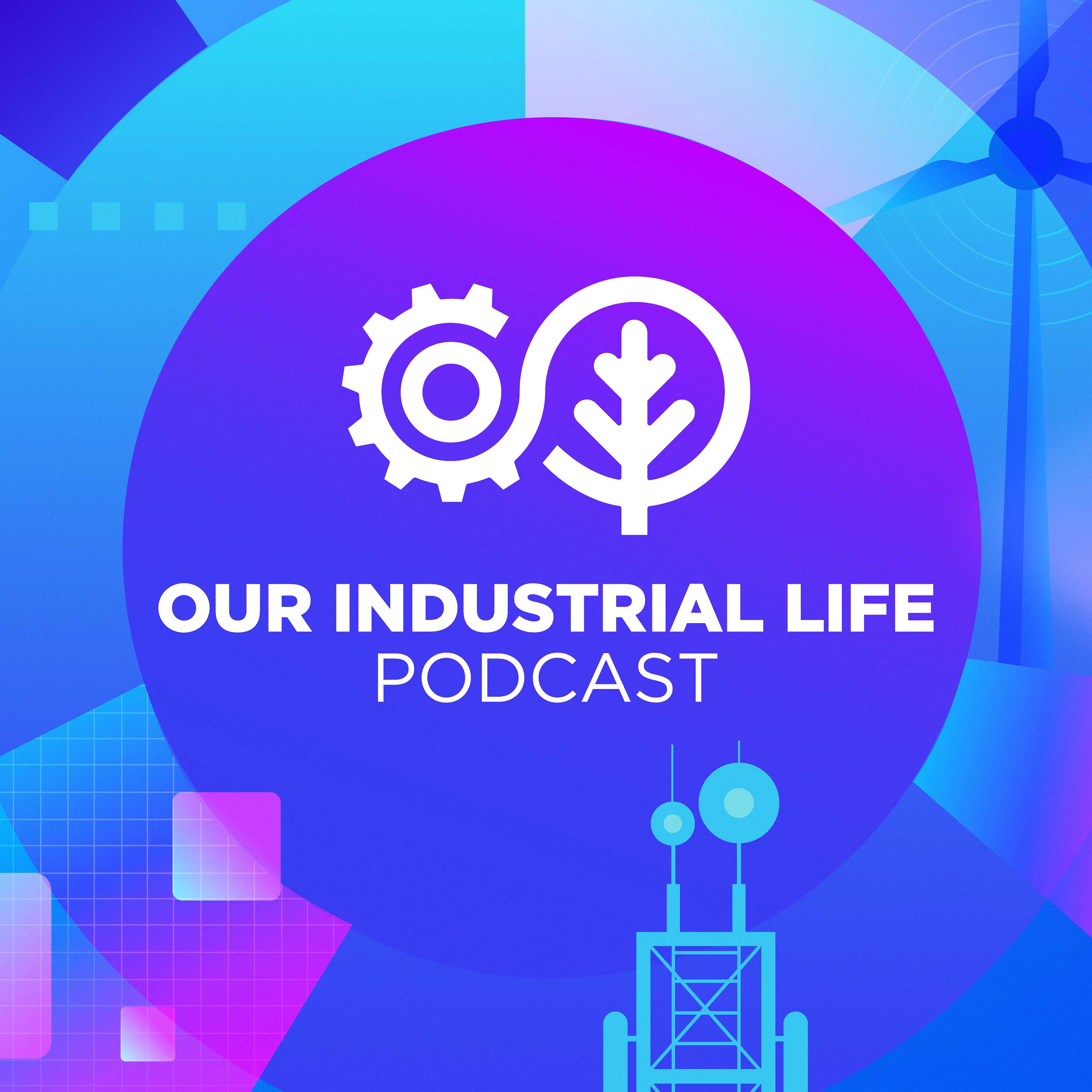
Kellogg's improves quality with sensor-based data
Guests: Emelio Anglés, Information Technology Engineer, Kellogg Company
Ted Combs, Industry Principal for Food, Beverage, and Consumer Packaged Goods (CPG), AVEVA
Information technology engineer Emelio Anglés of Kellogg Company is part of the Smart Factory project to digitalize all of Kellogg's manufacturing plants. He describes the different stages of this multi-year project to move from siloed PLCs using 5 different protocols to a single source of all data using a single protocol. Among the benefits he describes are a 50% reduction in mean time between failure on packing lines, a reduction of energy use over 15 years, and shortening production meetings from 45 minutes to as little as 15 minutes. Kellogg's can compare the efficiency of cereal plants from around the world using a single source of data.
Visit us at ourindustriallife.com
Our Industrial Life - Digitization of sensor-based data to reach Cement 4.0
Transcript
SUMMARY KEYWORDS
plants, data, people, operations, structure, cement, project, industry, plans, pi, consuming, units, collect, phase, turkey, specific, effect, decrease, equipment, calculations
00:08
Welcome everybody to Radio PI. Today we're going to be talking about, really about the most standard type of use of real time data. We typically see somebody who went from data everywhere in different formats, not able to compare like plants to like plants to a
If you like this episode you’ll love
Episode Comments
Generate a badge
Get a badge for your website that links back to this episode
<a href="https://goodpods.com/podcasts/our-industrial-life-577531/digitization-of-sensor-based-data-to-reach-cement-40-73543133"> <img src="https://storage.googleapis.com/goodpods-images-bucket/badges/generic-badge-1.svg" alt="listen to digitization of sensor-based data to reach cement 4.0 on goodpods" style="width: 225px" /> </a>
Copy