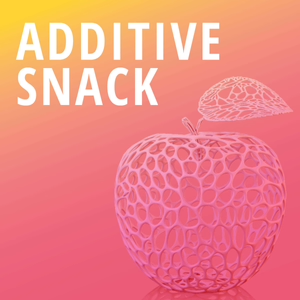
Fatigue & Fracture Behavior in AM Materials with Nima Shamsaei of Auburn University
04/16/24 • 30 min
The ultimate goal for additive manufacturing (AM) is for those creating, building, and designing for our future to reach for AM as another tool in their toolbox as easily as they would a traditional manufacturing method. To build this trust and knowledge of industrial 3D printing, countless hours of research are necessary.
To learn more about the research being performed at Auburn University that is shaping the future of AM, Host Fabian Alefeld speaks with a distinguished AM figure, Nima Shamsaei. Nima is a Philpott-West Point Stevens professor at Auburn University and Director of the National Center for Additive Manufacturing Excellence (NCAME). At NCAME, Nima and his team are at the forefront of research and technology and are actively studying the fracture and fatigue behavior of AM materials. In addition, a joint project with the US government and Auburn University is supporting manufacturers to create components for NASA.
Comments about the show or wish to share your AM journey? Contact us at [email protected]. The Additive Snack Podcast is brought to you by EOS.
Key Takeaways:
[1:39] An interest in mechanical properties led Nima from automotive to pushing the AM envelope with NASA.
[6:33] How Nima detects the fatigue behavior of additive materials.
[9:31] Three challenges of collecting and leveraging additive material data.
[16:19] When cost is not an issue, leveraging additive design maximizes its full potential.
[19:48] Part classifications are based on qualification complexities and the consequence of failure.
[23:21] A joint effort by the US government, Auburn University, and NASA support manufacturers to create parts NASA can use.
The ultimate goal for additive manufacturing (AM) is for those creating, building, and designing for our future to reach for AM as another tool in their toolbox as easily as they would a traditional manufacturing method. To build this trust and knowledge of industrial 3D printing, countless hours of research are necessary.
To learn more about the research being performed at Auburn University that is shaping the future of AM, Host Fabian Alefeld speaks with a distinguished AM figure, Nima Shamsaei. Nima is a Philpott-West Point Stevens professor at Auburn University and Director of the National Center for Additive Manufacturing Excellence (NCAME). At NCAME, Nima and his team are at the forefront of research and technology and are actively studying the fracture and fatigue behavior of AM materials. In addition, a joint project with the US government and Auburn University is supporting manufacturers to create components for NASA.
Comments about the show or wish to share your AM journey? Contact us at [email protected]. The Additive Snack Podcast is brought to you by EOS.
Key Takeaways:
[1:39] An interest in mechanical properties led Nima from automotive to pushing the AM envelope with NASA.
[6:33] How Nima detects the fatigue behavior of additive materials.
[9:31] Three challenges of collecting and leveraging additive material data.
[16:19] When cost is not an issue, leveraging additive design maximizes its full potential.
[19:48] Part classifications are based on qualification complexities and the consequence of failure.
[23:21] A joint effort by the US government, Auburn University, and NASA support manufacturers to create parts NASA can use.
Previous Episode
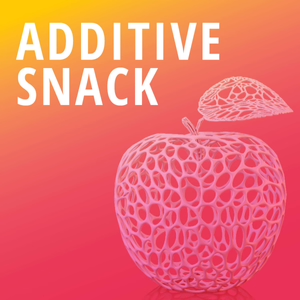
A.I. in Additive Manufacturing with Omar Fergani of 1000 Kelvin
It's clear that AI and additive manufacturing (AM) are a natural marriage of innovative technologies. As more companies focus on solutions that fortify the supply chain and increase the speed of engineering ingenuity, AM adoption will continue to accelerate.
Today, host Fabian Alefeld speaks with the co-founder and CEO of 1000 Kelvin, Omar Fergani. 1000 Kelvin is a company at the forefront of the AI-driven revolution in the AM industry. Omar explains the depths of the innovation driven by 1000 Kelvin, the pivotal role that AI plays in industrial 3D printing, and how the AMAIZE co-pilot helps engineers to reduce design time and engineer onboarding.
Comments about the show or wish to share your AM journey? Contact us at [email protected]. The Additive Snack Podcast is brought to you by EOS.
Key takeaways:
[1:18] 1000 Kelvin’s mission and how it plans to solve additive manufacturing’s biggest challenges.
[6:26] How implementing a materials processing discipline will move additive manufacturing to serial production.
[10:41] 1000 Kelvin’s AMAIZE is a co-pilot engineering tool and thermal management platform.
[12:58] On a macro level, AMAIZE helps to onboard new engineers.
[19:45] How the co-pilot integrates into the design workflow.
[22:09] Business use cases support the growth of AM spare parts and fortify the supply chain.
[26:03] The limitations and advantages of AI in AM.
Next Episode
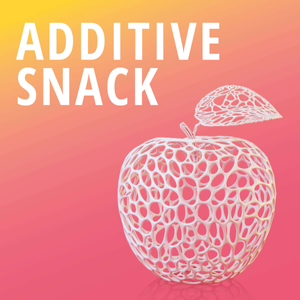
Personalized Spinal Bracing Made Reality with Additive Manufacturing
Additive manufacturing (AM) isn't just shaping the future of medical devices, it is actively changing lives. As it opens new possibilities for patient care around the globe, innovative 3D design solutions are raising the bar for patient comfort and satisfaction.
Today, Host Fabian Alefeld speaks with Lisa Tweardy, CEO of MIGN, a company leading the charge in innovative spinal brace technology that leverages industrial 3D printing. We have Dr. Baron Lonner, a leader in minimally invasive scoliosis surgery, Isabelle (Liz) Rauch, Orthotist for Dr. Lonner of Orthotic Consultants, and Livi Lasner, founder of Save a Spine, an organization she started to connect those who need spinal braces with the financial support to obtain them. Together they explore how additive manufacturing is revolutionizing not only healthcare but spinal health from a personal and technological perspective.
Comments about the show or wish to share your AM journey? Contact us at [email protected]. The Additive Snack Podcast is brought to you by EOS.
Key takeaways:
[1:48] A patient's physical and psychological comfort are essential components of spinal brace design.
[9:36] MIGN is the first and only company to personalize orthopedic bracing at scale.
[15:13] How additive technology allows Dr. Lonner to approach scoliosis treatment differently.
[19:31] An end-to-end digital design workflow allows MIGN to send production requirements anywhere in the world.
[22:12] The mission of the Save a Spine organization.
Resource links:
If you like this episode you’ll love
Episode Comments
Generate a badge
Get a badge for your website that links back to this episode
<a href="https://goodpods.com/podcasts/additive-snack-376606/fatigue-and-fracture-behavior-in-am-materials-with-nima-shamsaei-of-au-53840266"> <img src="https://storage.googleapis.com/goodpods-images-bucket/badges/generic-badge-1.svg" alt="listen to fatigue & fracture behavior in am materials with nima shamsaei of auburn university on goodpods" style="width: 225px" /> </a>
Copy